Quality Systems & Risk Management
AAMI's quality systems and risk management training provides medical device design and manufacturing professionals the tools and knowledge to maintain regulatory compliance with all applicable FDA and ISO requirements.
Combination Products: A Risk-Based Approach (September 2025)
Sep 9 to Sep 12, 2025
Quality Systems
Design Control Requirements - Integrating the Quality System Regulation (Sept25)
Sep 9 to Sep 11, 2025
Quality Systems
Integrating Risk Management into the Product Life Cycle (Oct25)
Oct 1 to Oct 3, 2025
Quality Systems
Design Control Requirements - Integrating the QMSR (Dublin IRE | Oct 2025)
Oct 7 to Oct 9, 2025
Quality Systems
The Changing AI/ML Medical Device Regulatory Landscape (October 2025)
Oct 9 to Oct 9, 2025
Software/Cyber
Transitioning to the FDA Quality Management System Regulation (QMSR) (Oct 2025)
Oct 14 to Oct 16, 2025
The Quality Management System Regulation (QMSR) (Amsterdam | Nov 2025)
Nov 3 to Nov 7, 2025
Quality Systems
The Quality Management System Regulation (QMSR) (November 2025)
Nov 17 to Nov 21, 2025
Quality Systems
Process Validation Requirements & Industry Practices (Dec25)
Dec 1 to Dec 3, 2025
Quality Systems
Design Control Requirements - Integrating the Quality System Regulation (Dec25)
Dec 2 to Dec 4, 2025
Featured Courses
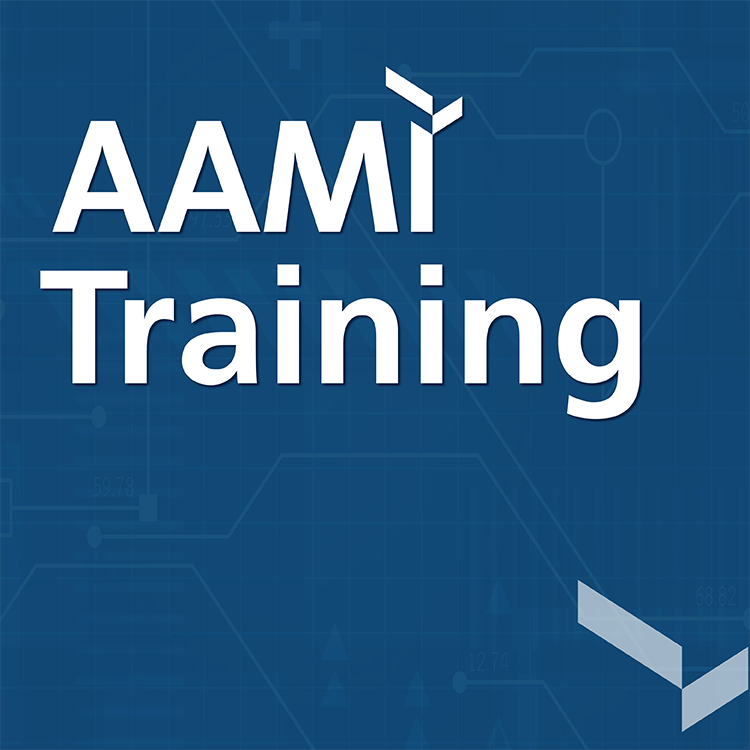
Quality Systems & Risk Management
AAMI Training Cost Rica
In 2025, AAMI Training is bringing world-class education to Costa Rica with three in-person courses tailored for professionals in the growing medical device industry.
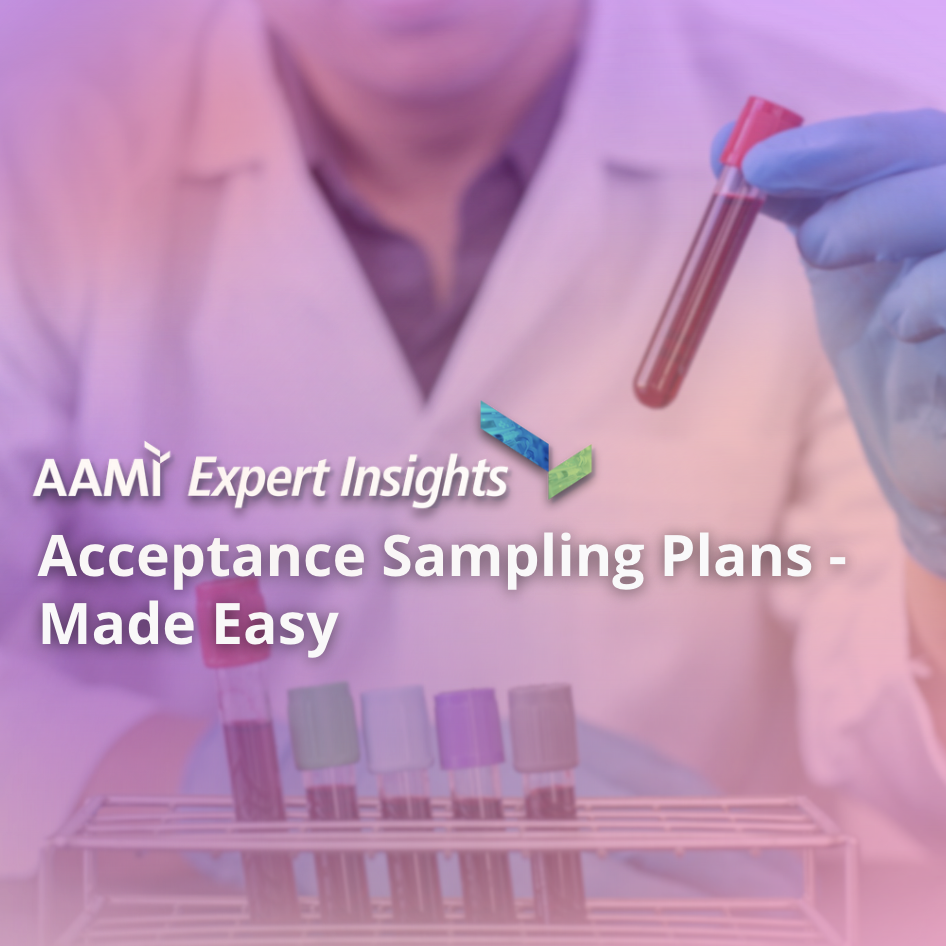
Quality Systems & Risk Management
Acceptance Sampling Plans - Made Easy
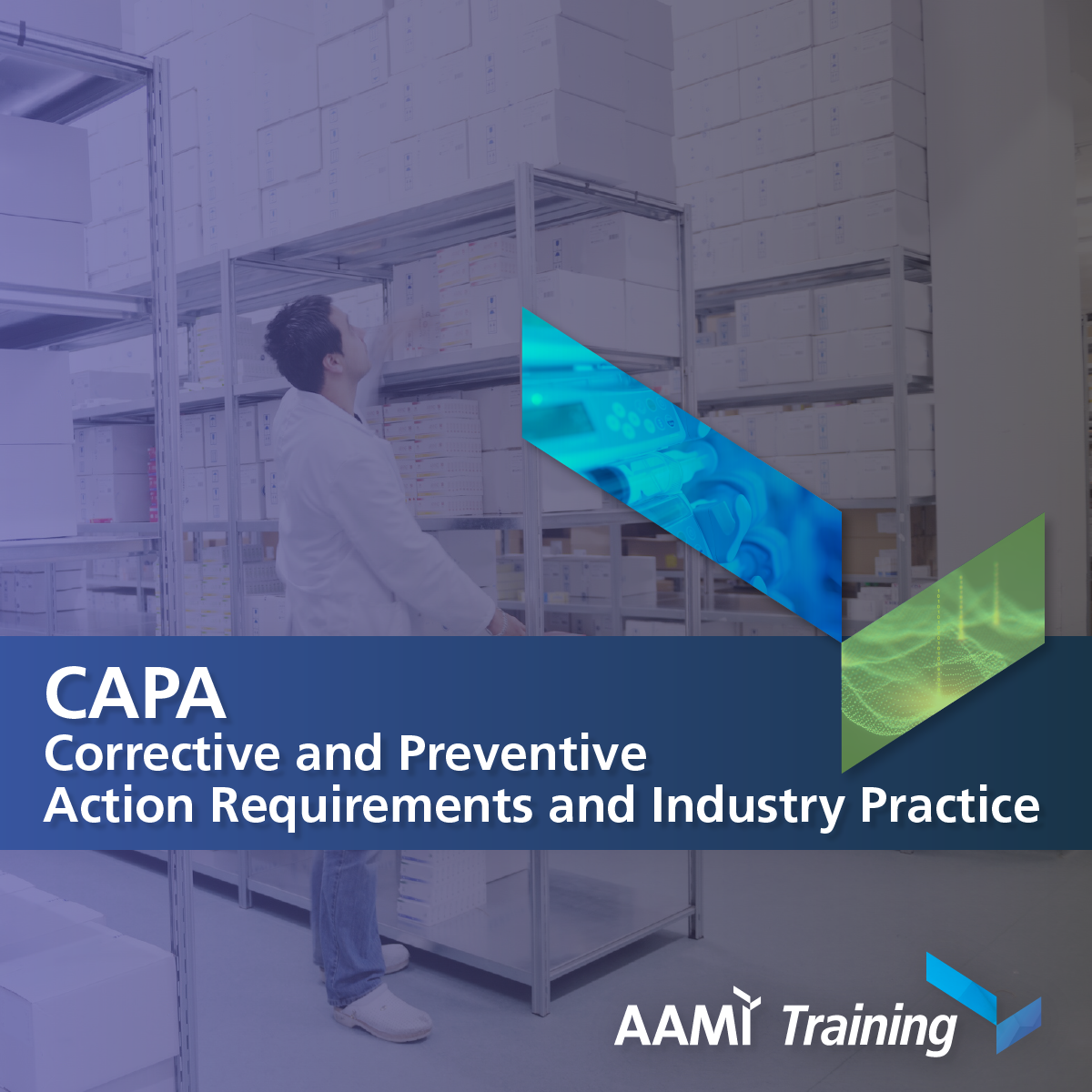
Quality Systems & Risk Management
CAPA: Corrective and Preventive Action Requirements and Industry Practice
Quality Systems & Risk Management
Design Control Requirements - Integrating the QMSR (Dublin IRE | Oct 2025)
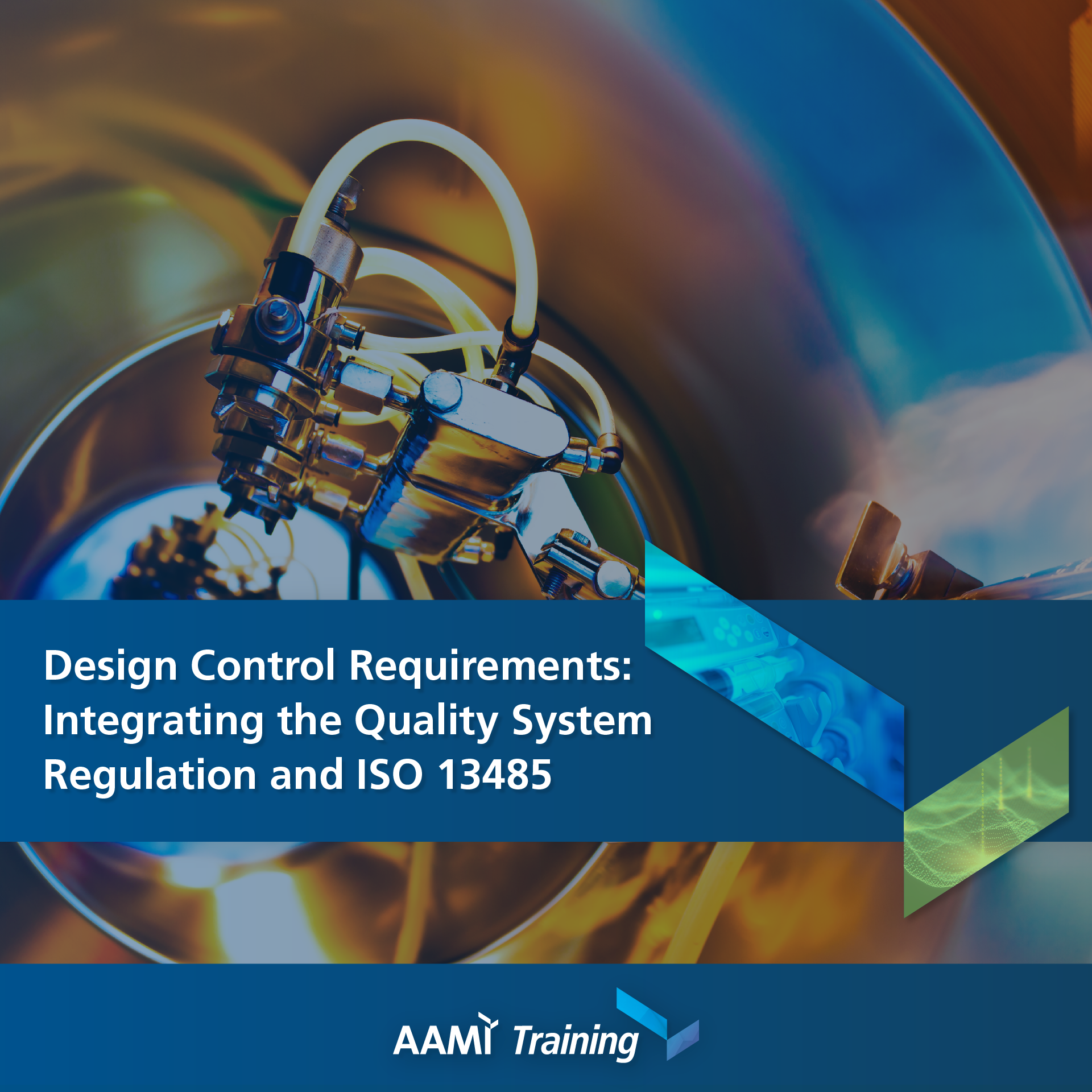
Quality Systems & Risk Management
Design Control Requirements - Integrating the Quality System Regulation
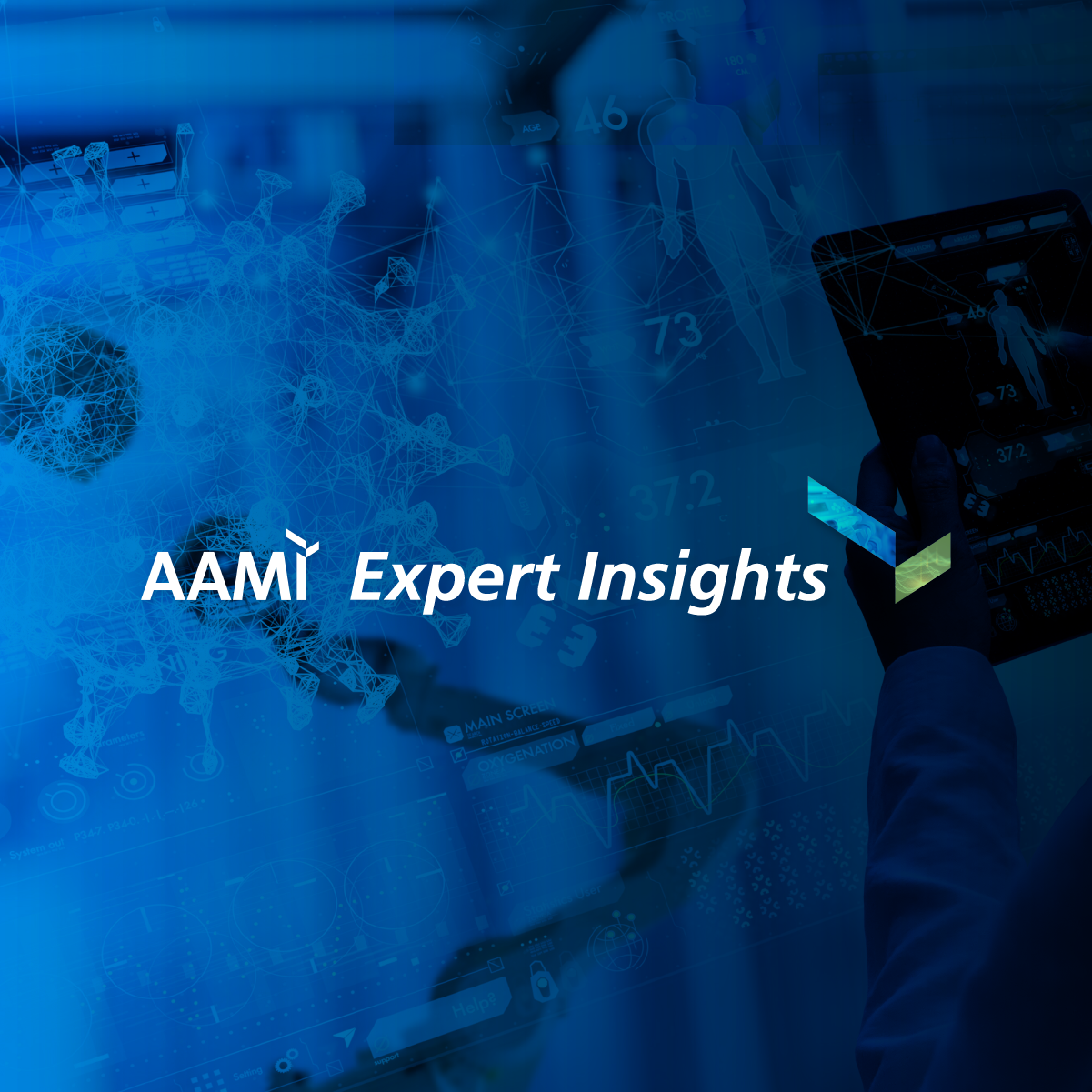
Quality Systems & Risk Management
Design of Experiments: A Faster, Better, Cheaper Methodology
People involved with designing and implementing production processes are often challenged with how to characterize their product or processes and, then, optimize results. This is especially true for medical device and pharmaceutical firms. What parameters are key to quality? How do we quickly and efficiently identify these parameters and decide on strategies to optimize quality? This webinar is focused on a “Faster, Better, Cheaper” methodology.
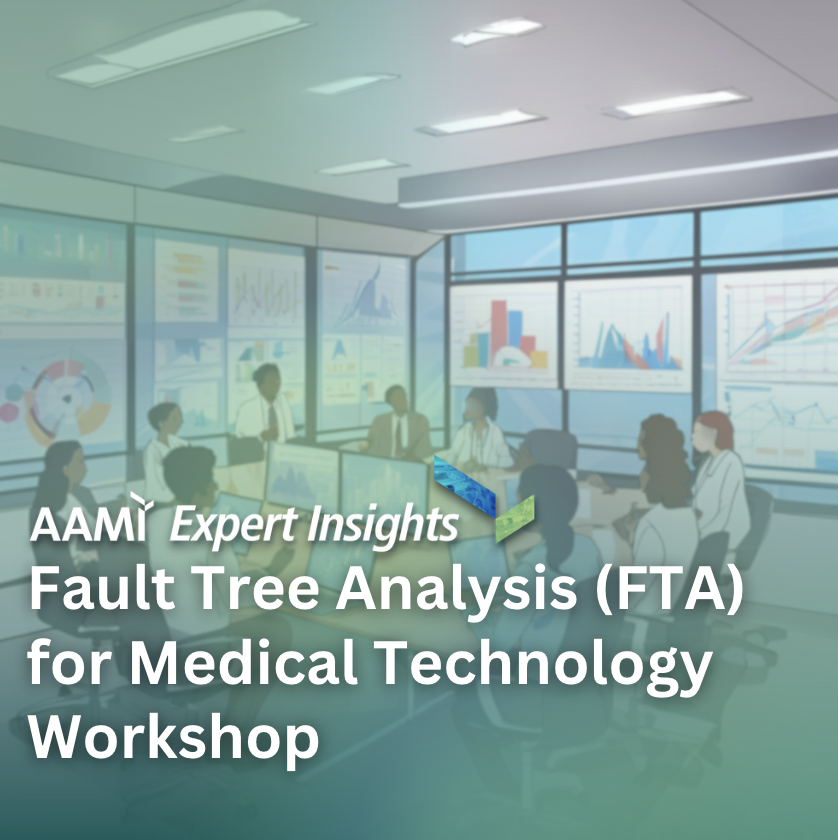
Quality Systems & Risk Management
Fault Tree Analysis for Medical Technology Workshop
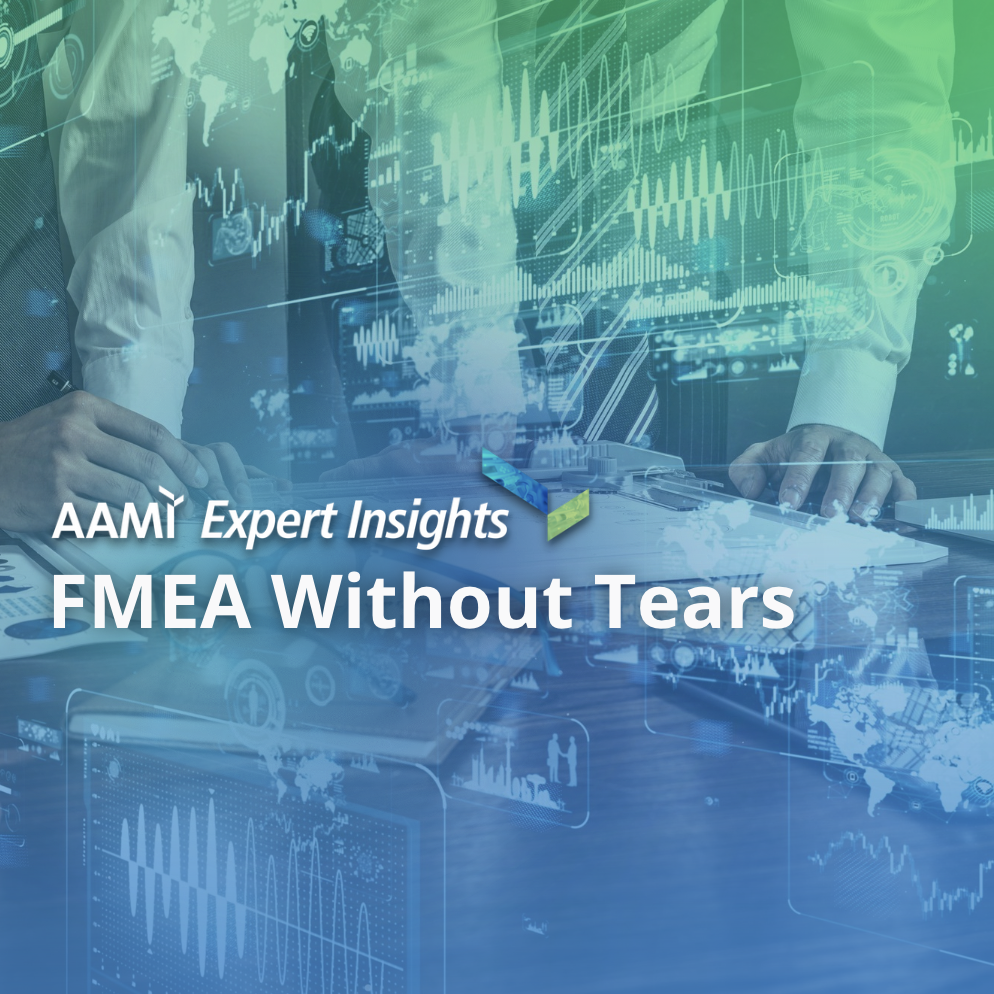
Quality Systems & Risk Management
FMEA Without Tears
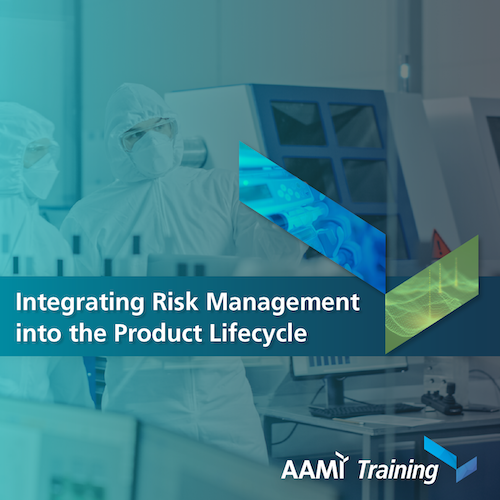
Quality Systems & Risk Management
Integrating Risk Management into the Product Life Cycle
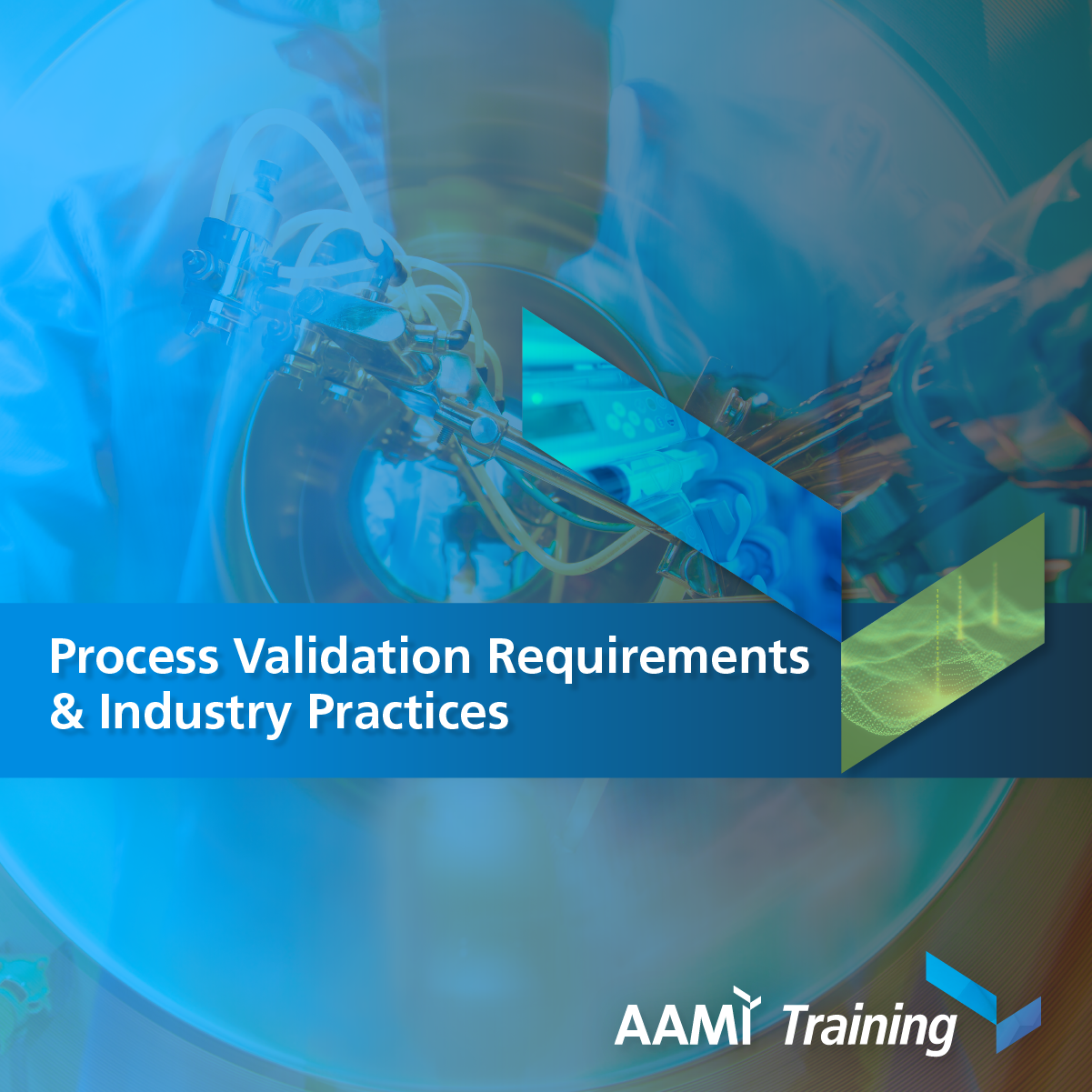
Quality Systems & Risk Management
Process Validation Requirements & Industry Practices
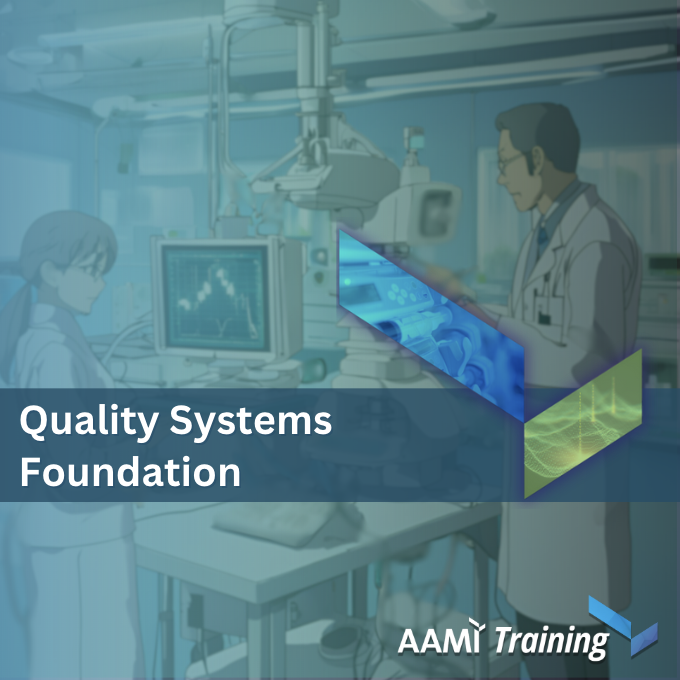
Quality Systems & Risk Management
Quality Systems Foundation
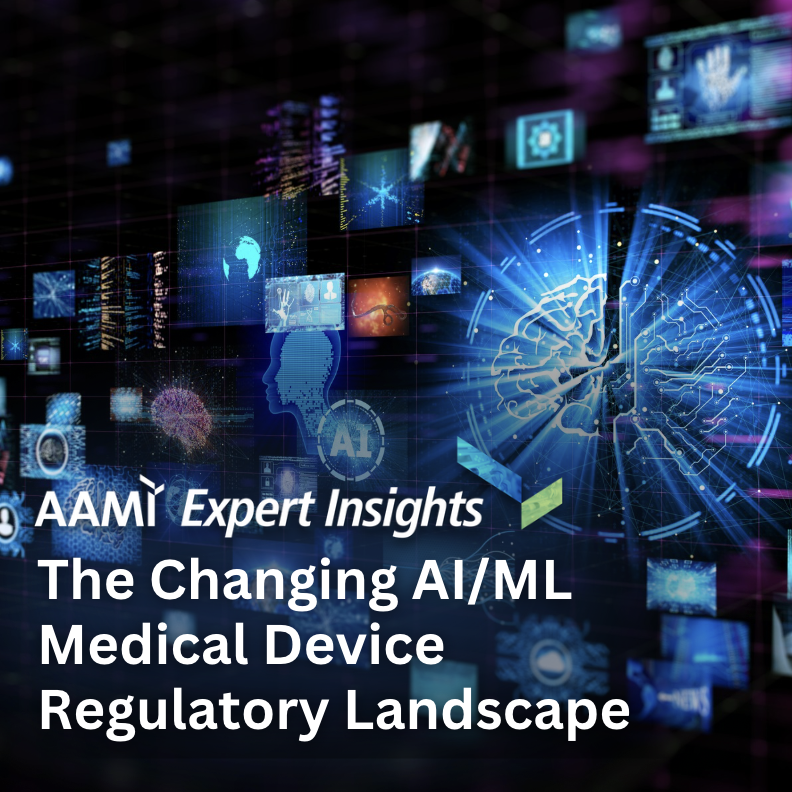
Quality Systems & Risk Management
The Changing AI/ML Medical Device Regulatory Landscape
This training will describe current and upcoming regulatory trends in AI-enabled medical devices such as software as a medical device (SaMD). This training will similarities and differences in regulations across jurisdictions such as the USA FDA, EU, UK, ASEAN region, Australia, and Canada. It will cover impacts to manufacturers’ device design, labeling, QMS and cybersecurity processes.
Quality Systems & Risk Management
The Quality Management System Regulation (QMSR) (Amsterdam | Nov 2025)
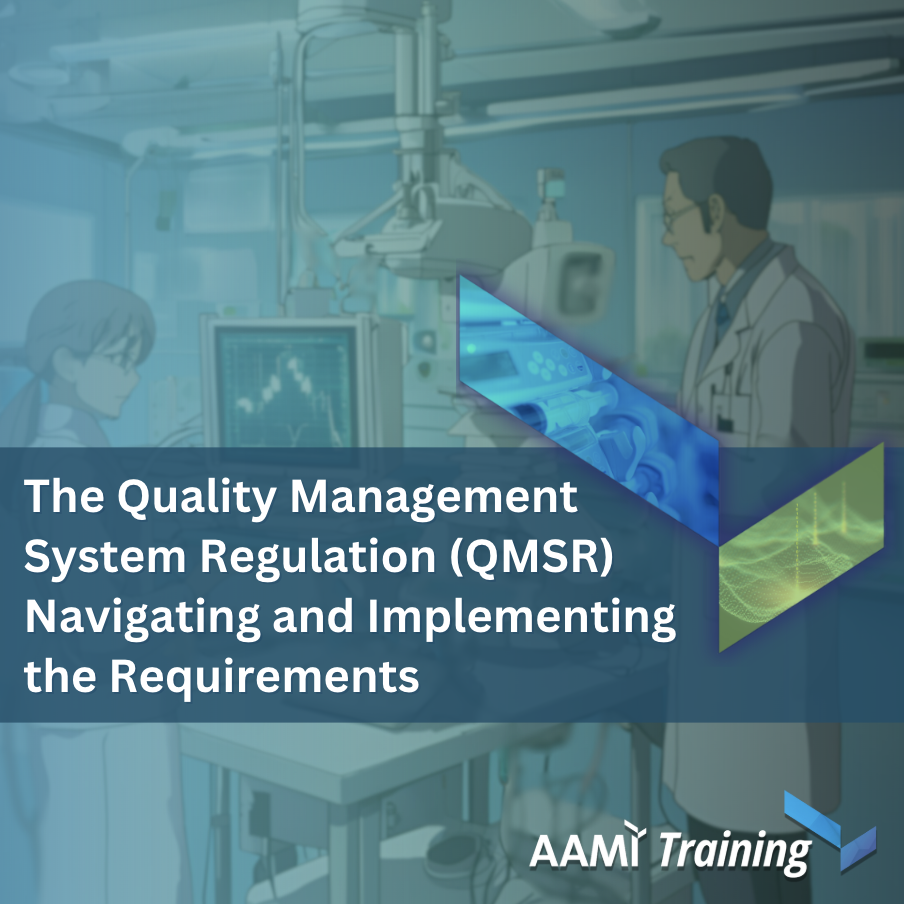
Quality Systems & Risk Management
The Quality Management System Regulation (QMSR): Navigating and Implementing the Requirements
AAMI’s world class quality management system course has been updated for the upcoming FDA QMSR regulations!
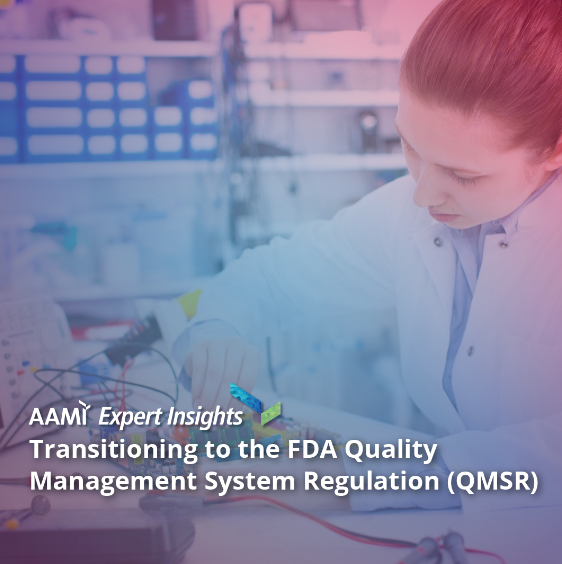
Quality Systems & Risk Management
Transitioning to the FDA Quality Management System Regulation (QMSR)
The FDA recognizes the benefits of harmonization with other regulatory authorities, and it has determined that ISO 13485:2016, the globally recognized standard for a medical device organization’s QMS, is substantially similar to the current version of 21 CFR Part 820 which became effective in 1996.
Faculty
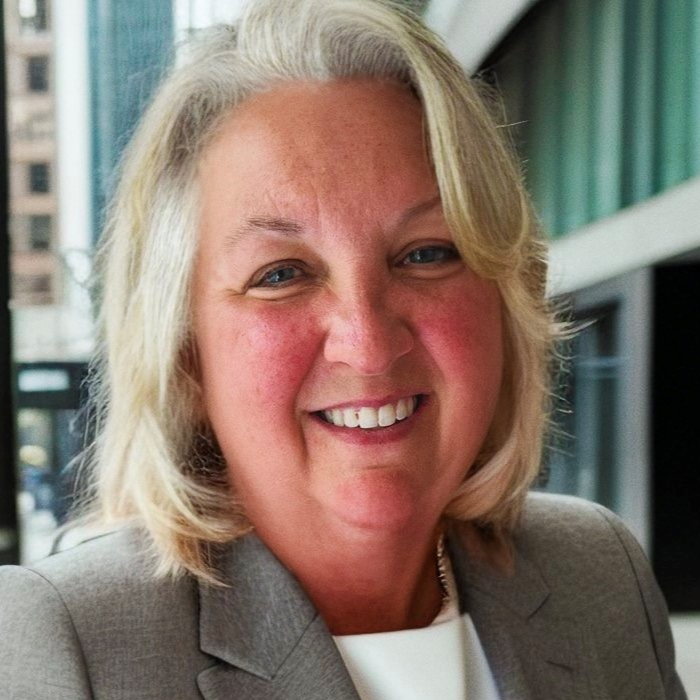
Tiea Theurer
Tiea is a quality and regulatory professional with experience in auditing, QMS, and medical writing relative to design and risk management. In her 20+ years of experience in the medical device industry, she has served in roles as project manager and design quality engineer. In these roles, Tiea acted as a change agent in QMS and DHF/DMR remediation efforts to resolve FDA 483 and notified body nonconformances for companies who were under warning letters or consent decree.
Tiea has performed 100+ audits as a Lead auditor for Notified Bodies to assess compliance with quality management system (QMS) standards (ISO 9001/13485) and regulatory requirements for the USA 21CFR820, EU (MDD/MDR, IVDD/IVDR), Canada (CMDCAS), and MDSAP jurisdictions (Australia-TGA, Brazil-Anvisa, Canada-CMDR, Japan-MHLW, and US-FDA). Tiea has experience with various technology types, such as, but not limited to software as a medical device, sterilization and sterile barrier systems, plastics, mechanical and electrical equipment and chemicals.
Based on these, Tiea is qualified for auditing most medical and IVD devices, with the exception of implantable devices. Tiea has working relationships with several private clients which required gap assessments and remediation activities of quality and regulatory documents relative to industry standards and country regulations.
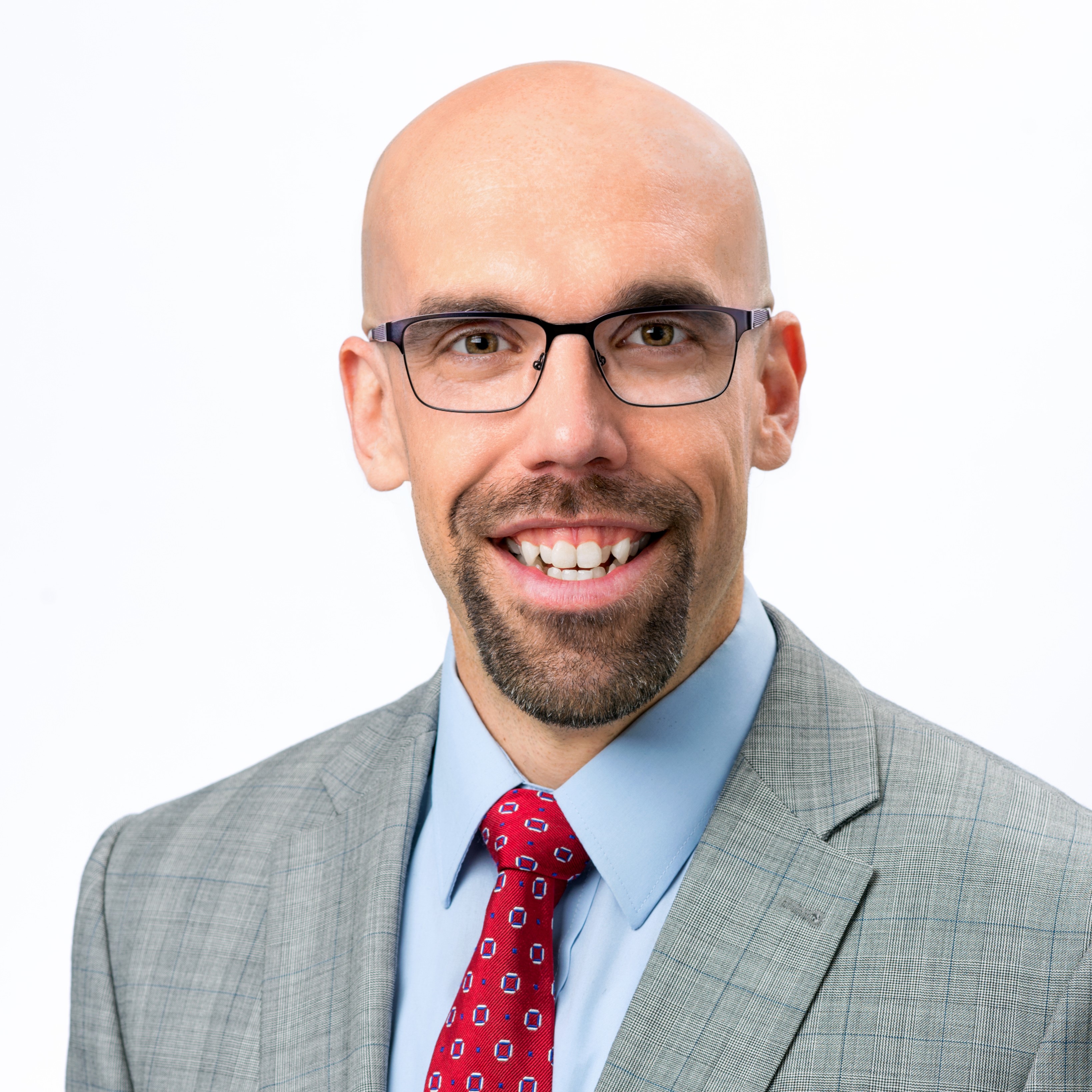
Mike Ziemelis
Mike Ziemelis currently works with Stryker in the Emergency Care business unit as a Senior Director within Research and Development. Mike and his teams are focused on the development of AEDs, defibrillators, patient monitors, and other therapeutic devices used within the emergency medical services space, hospitals, and the community.
Prior to working in his current role, Mike has held multiple roles within Stryker supporting different businesses that focus on various class I and class II medical devices. Mike has over 18 years of medical device experience in R&D, premarket RAQA, business development, and advanced manufacturing.
Mike is an experienced trainer within Stryker and with AAMI. As an active AAMI faculty member, Mike teaches the Quality System Requirements and Design Controls courses. Mike earned his Bachelors of Science in electrical engineering and his Masters of Science in Engineering management from Western Michigan University.
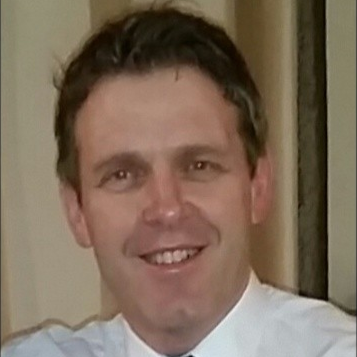
Gerard Manley
Gerald (Ger) Manley is a medical device and pharma industry consultant with +20 years’ industry experience and is owner & Director of G&C Creations Ltd.
G&C Creations ltd was founded in 2004. G&C Creations ltd has provided consultancy services in the medical device and pharmaceutical sector working for a host of different companies with considerable market share in the diagnostic, general medical devices, implants, API’s, Biologists etc. G&C Creations ltd has extensive experience in New product introduction, technical transfers, product launches, process improvement, Lean, end to end supply chain, Design Controls Quality system requirements, outsourced manufacturing and implementing full and partial Quality management systems.
In 2009 to complement the consultancy division of the business, G&C Creations added contract technical services which has +100 technical professionals supporting projects with various clients around Ireland and Europe
Qualification 93-95: National Cert. Electronics Eng
Institution - Tralee Institute of technology Ireland.
Qualification: 95-96 Diploma Mechanical and Electronic Engineering
Institution - Tralee Institute of technology Ireland.
Qualification: 96-98 Bachelor of Engineering Hons (1:1) Mechanical & Production Engineering
Institution - University of Limerick Ireland.
Qualification: 2000 National Cert. EH&S - Waterford Institute of technology Ireland.
Faculty Member of the Association for the advancement of medical instrumentation (AAMI) – Training Partner to the FDA
AAMI certified faculty for the following;
- Process Validation
- Design Controls
- QSR for 21CRF820 & ISO13485:2016
- Risk Management
Certified Lead auditor ISO13485:2016
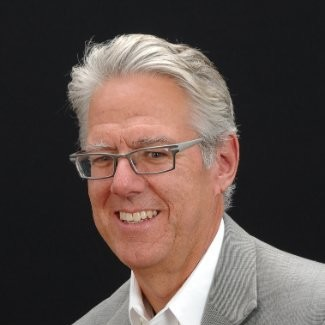
Andy Snow
Andrew has almost 40 years of experience managing quality, design and development for large medical device companies, start-ups and contract manufacturers. He has proven expertise in quality systems, risk management, design controls, requirements management, software life cycle processes and reliability engineering. He has a proven track record for developing risk management processes and systems for software and hardware device using ISO 14971. He has leveraged this expertise to help companies improve compliance, product quality and reliability. He has a BS degree in Biology from Fort Lewis College, a master’s degree in engineering from Northwestern and a graduate certificate in Systems Engineering from University of Arizona.
Andrew is currently a Quality and Regulatory Consultant to the Medical Device Industry Specializing in Improving Quality Management Systems. His skills and expertise include:
· Medical Device Quality and Regulatory – FDA 21 CFR part 820, Quality Systems Regulations and ISO 13485 Quality Management Systems for Medical Devices.
· Recognized industry expert in Risk Management using ISO 14971 and including integration with t=requirements for IEC 60601 and IEC 62304.
· Requirements lifecycle management including eliciting/formulating requirements, traceability and configuration management across the lifecycle.
· Design Verification, Design Validation planning and execution
· Process development, characterization and validation planning and execution.
· Supplier quality management and purchasing controls.
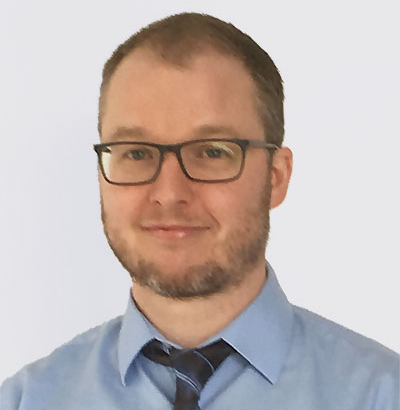
Sebastian Clerkin
Seb Clerkin is the founder of GMP Advisory Services, cofounder of CQT Solutions and a faculty member of the Association for the Advancement of Medical Instrumentation (AAMI). He currently provides quality system and regulatory consultancy to multiple clients within the Medical Device sector.
He has an excellent track record in providing consultancy, training and auditing. His main expertise is in the areas of Regulations, Quality Management systems, Design Controls, Software and Process Validation. He is a IRCA certified lead auditor and provides auditing services to multiple clients.
He has published articles in peer-reviewed journals on topics such as cleaning validation. He has a PhD from the University of Bristol, which involved studying the toxicological and biological effects of prosthetic implants and is a member of AAMI and RAPS.
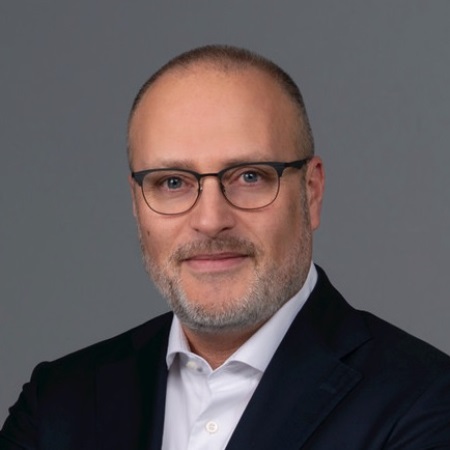
Mario Wijker
Mario Wijker is a seasoned quality and regulatory professional with over 30 years of experience in the medical device and in-vitro diagnostics industry. He started his career performing human genetic testing at the Free University of Amsterdam in The Netherlands.
Since then, he has held several positions in small, medium and large in-vitro diagnostics and medical device companies in all product classifications. In addition to roles in business development and strategic marketing, he has led global quality and regulatory organizations for 15 years and has developed and implemented quality systems in several companies.
He is an expert in quality remediation program and translating quality and regulatory requirements into actionable deliverables for a corporation. He is a certified ISO 13485:2016 and MDSAP lead auditor and has a degree in Biochemistry and Genetics.
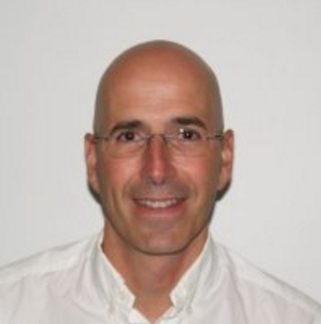
Philippe Joly
client firms to establish cGMP/QSR-compliant quality systems or to improve the efficiency of the existing ones. He has 10 years of experience in developing and delivering training on cGMP/QSR. Prior to this job, Philippe Joly has been involved in sales, marketing and product development for two international companies involved in the biopharmaceutical and medical device market.
Philippe Joly has a MS degree in Biochemistry and Microbiology and a Master's in Management and Marketing. He has led several workshops and task forces (Personnel qualification, cleaning validation, validation of computerized systems, risk management) for the two main French Pharmaceutical societies.
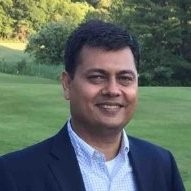
Samir Paliwal
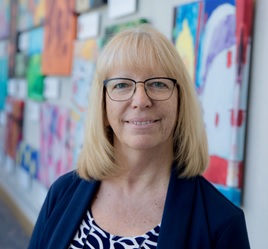
Tina Krenc
Tina is the Principal Consultant for KTA Compliance Consulting. She has over 40 years of medical device industry experience in a variety of organizations and functions including IVDs, software, hardware, combination products, and implantable medical devices. She has led employees in research and development, clinical research, operations technical support, and has over 25 years of quality assurance experience in multiple quality organizations.
As a consultant, Tina assists organizations with developing or improving their QMS to support the safety and effectivenss of their medical devices.
Tina serves as member of TC 210 ISO/IEC/ JWG1 on Application of Risk Management to Medical Devices and is the co-lead of the US TAG for ISO 14971. Tina is also a member of IEC SC 62A - Common aspects of electrical equipment used in medical practice. In addition, she is the ISO TC210 liaison for Risk Management subject expertise to ISO/TC212 - In-vitro Diagnostics Technical Committee.
Tina received a Master of Science in Product Design and Development from Northwestern University School of Engineering in 2006.
Tina has taught risk management for several organizations including Northwestern University Master of QARA program and AAMI. She teaches several AAMI University courses including Design Control, Quality Management Systems, Process Validation, and Risk Management.
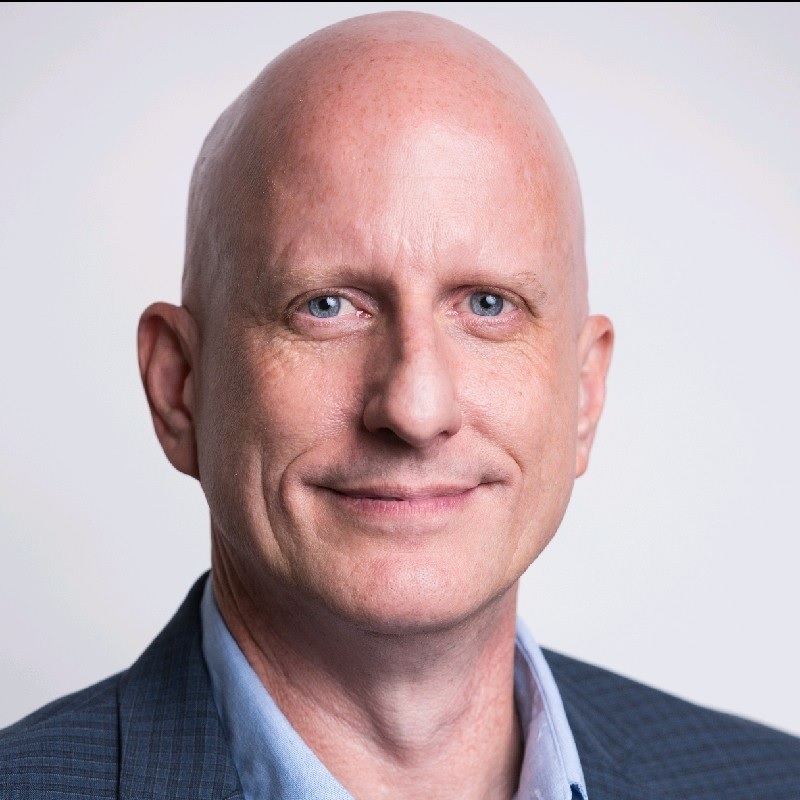
David Nelson
David has a background in Software Engineering and has 26+ years of experience developing and validating Medical Devices. He currently is an Associate Software Director for Boston Scientific Neuromodulation. His responsibilities include managing all aspects of software development and validation including security risk. In addition, David is a faculty member at AAMI and has been developing and instructing courses for more than 12 years.
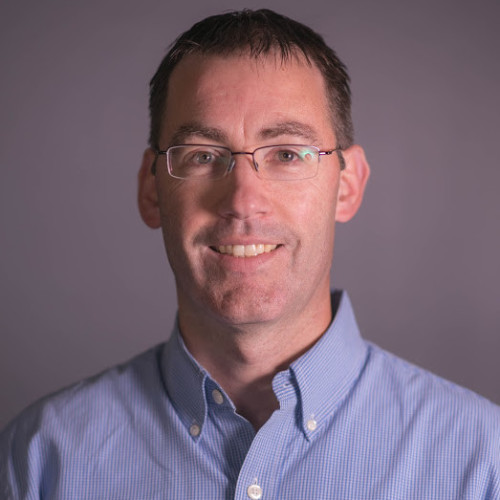
Eric Kruschke
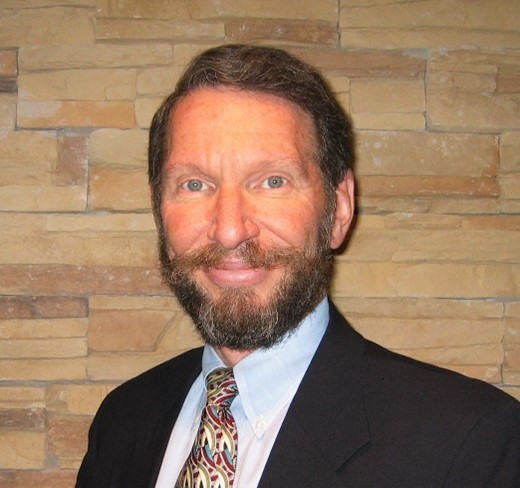
Peter Knepell
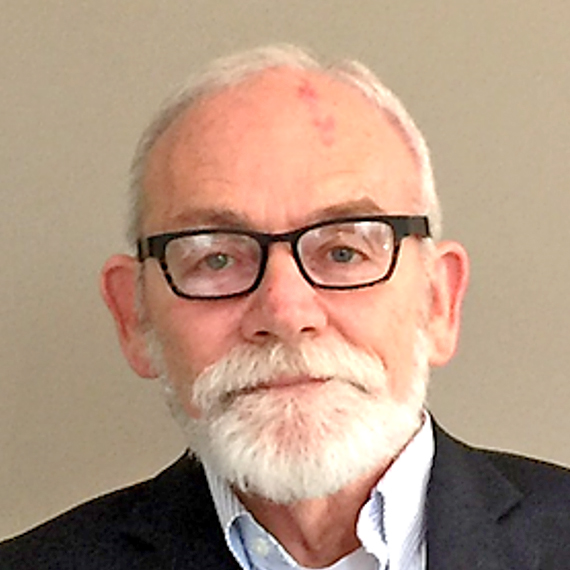
Jack Ward
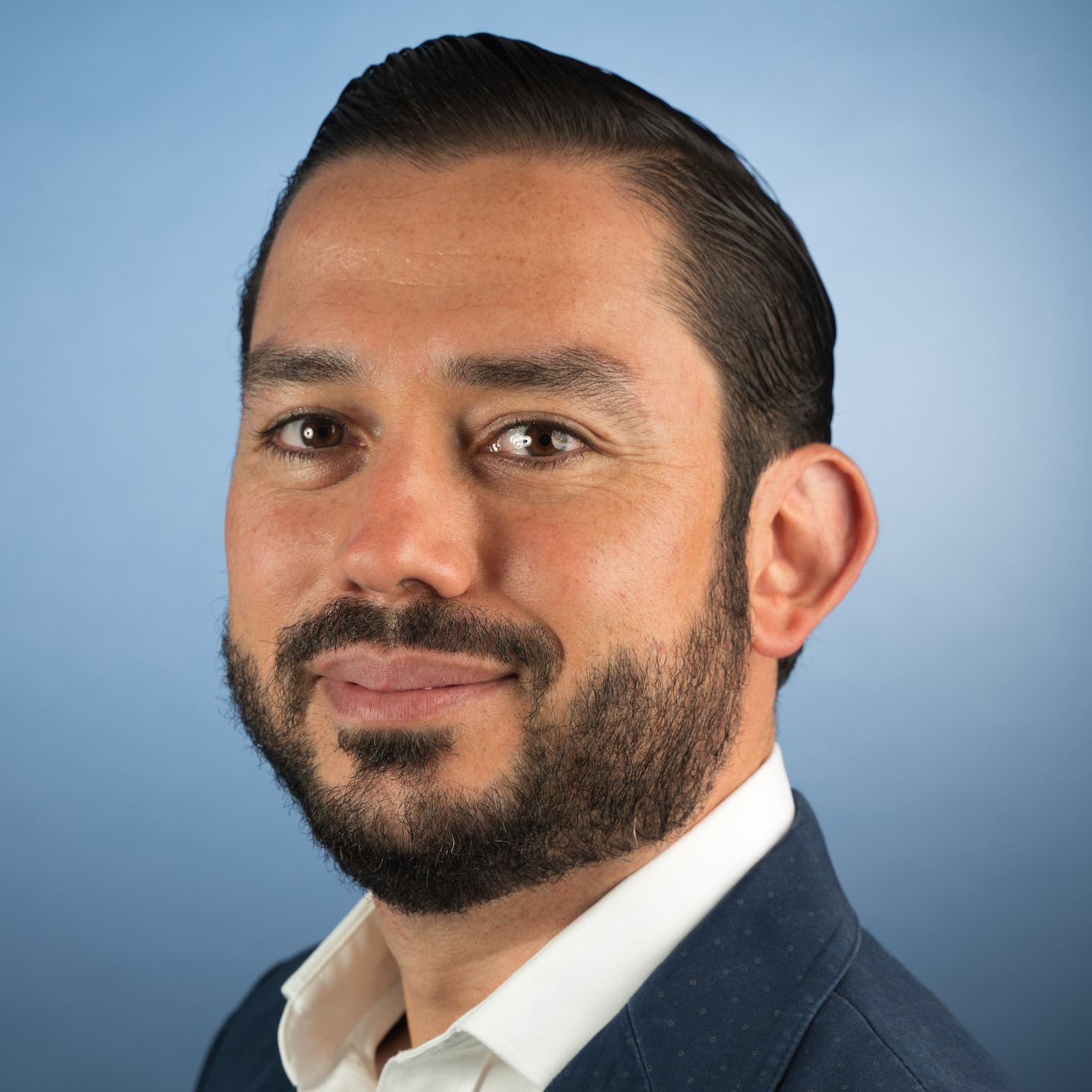
Pablo Montero
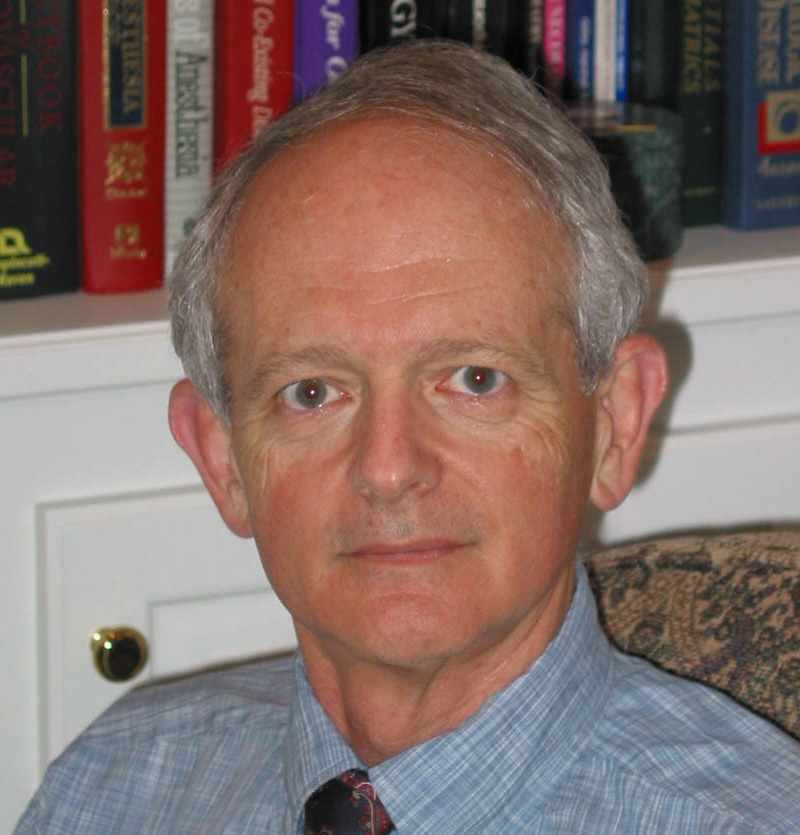
Ed Bills
During his career in medical devices, Mr. Bills has held a number of quality and regulatory affairs positions for major medical device companies, including a period as Corporate Director of Risk Management. He has over 39 years’ experience in the field of quality and regulatory affairs, including time as Director of Quality and Regulatory concurrently for four US sites. Currently he consults and provides training in the area of medical device quality, regulatory and risk management. With Stan Mastrangelo, he co-edited Lifecycle Risk Management for Healthcare Products: From Research Through Disposal published by PDA and has written extensively in the area of quality, regulatory, and risk management for medical devices and combination products.
ASQ has awarded Mr. Bills with Fellow status as well as Certified Quality Engineer, Certified Quality Auditor, Certified Manager of Quality and Organizational Excellence, and he is Regulatory Affairs Certified by the Regulatory Affairs Professionals Society. In his career he has given presentations nationally and internationally in the field of quality management and risk management.
Additionally, Mr. Bills serves in international standards work, assisted in completing the revision of the third edition of ISO 14971 risk management standard and the guidance ISO TR 24971:2020 as an international member of the technical committee. He also serves on the US national committee for the medical devices quality system standard, ISO 13485, as well as the medical bed standards, IEC 60601-2-52, IEC 60601-2-89, and the AAMI technical committee CP contributing to the combination products risk management guidance, AAMI TIR 105.
Mr. Bills has recently taught as part of the Quality Science Education program at The Wistar Institute, and LaSalle University under the Pathways for Patient Health program. He has previously taught at University of Southern California, the University of Washington, and Purdue University Southeast. He was also adjunct faculty at Virginia Tech in the Health Products Risk Management Graduate Program and assisted in development of that program.
Recently, Mr. Bills joined Gessnet as a Technical Advisor. He also serves on the Advisory Board of Product.
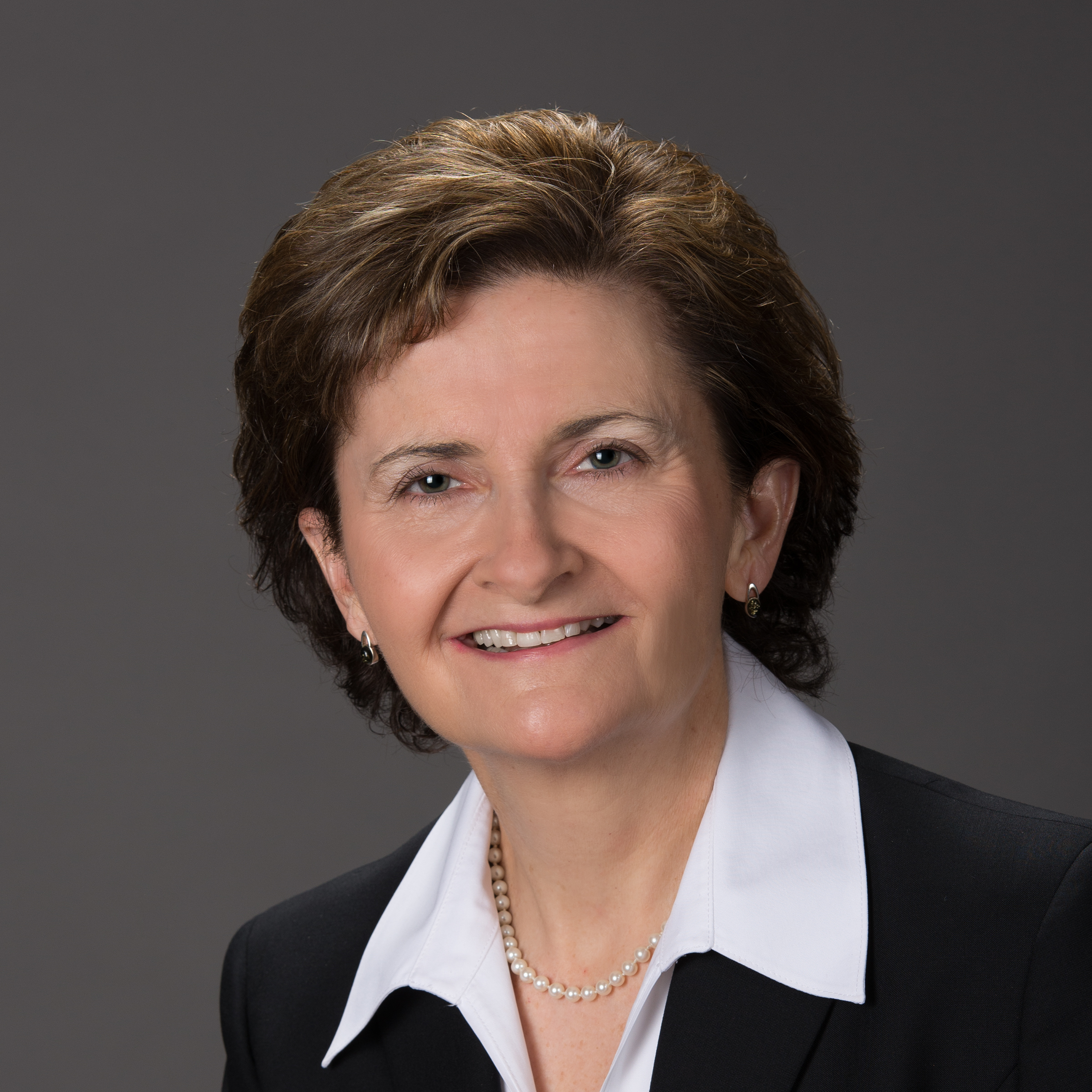
Annette Hillring
Annette Hillring has been an independent regulatory affairs consultant since 1998. Prior to consulting, she worked in the medical device industry with ophthalmic, cardiovascular and general hospital devices. She has over 40 years of experience in regulatory affairs, quality systems, clinical affairs and compliance. Her worldwide regulatory affairs responsibilities have included FDA and worldwide device submissions, Quality System Regulation compliance, ISO 13485 conformance, interpretation of all FDA regulations and policies, regulatory representation on new product development teams, due diligence assessments and product liability. She has also served as an expert witness for FDA and has extensive experience in software related FDA/industry guidance and standards-setting activities.
Ms. Hillring is Regulatory Affairs Certified and holds BA degrees in biology, microbiology and secondary science education
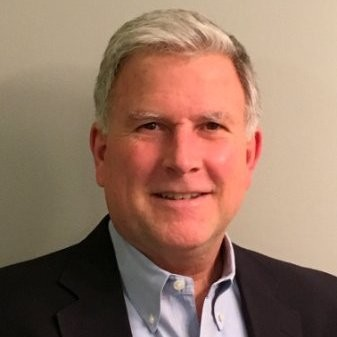
Mark Walker
Mr. Walker has been an instructor for the Association for the Advancement of Medical Instrumentation (AAMI) since 2012 which develops training and guidance with FDA for the use of medical devices. He currently serves on AAMI Medical Device Software Committee. Mr. Walker was a contributing author for The Quality System Compendium: CGMP Requirements and Industry Practice, Fourth Edition and also co-authored “Risk Management Tools” (Chapter 2) in the book “Risk Management Applications in Pharmaceutical and Biological Products Manufacturing”, published by John Wiley & Sons, Inc.
Mr. Walker has a Bachelor of Science degree and an Associate of Engineering degree in chemical engineering technology. In his free time, he volunteers with county emergency rescue service agencies providing technical rescue, emergency medical services and computer systems support.
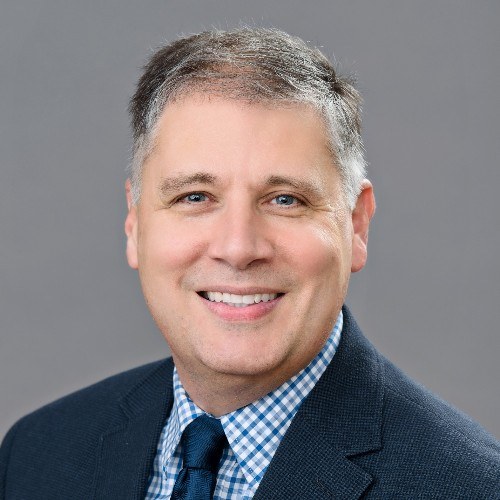
Mark Durivage
Mark Allen Durivage has worked as a practitioner, educator, and consultant. He is Managing Principal Consultant at Quality Systems Compliance LLC, ASQ Fellow, SRE Fellow, and an Expert Faculty Member for AAMI. He holds several certifications including CRE, CQE, CQA, CSQP, CSSBB, RAC (Global), and CTBS. Durivage has written several books available through ASQ Quality Press, published articles in Quality Progress, and is a frequent contributor to Life Science Connect.
Mark primarily works with companies in the FDA regulated industries (medical devices, human tissue, animal tissue, and pharmaceuticals) focusing on quality management system implementation, integration, updates, and training. Additionally, he assists companies by providing internal and external audit support as well as FDA 483 and Warning Letter response and remediation services.
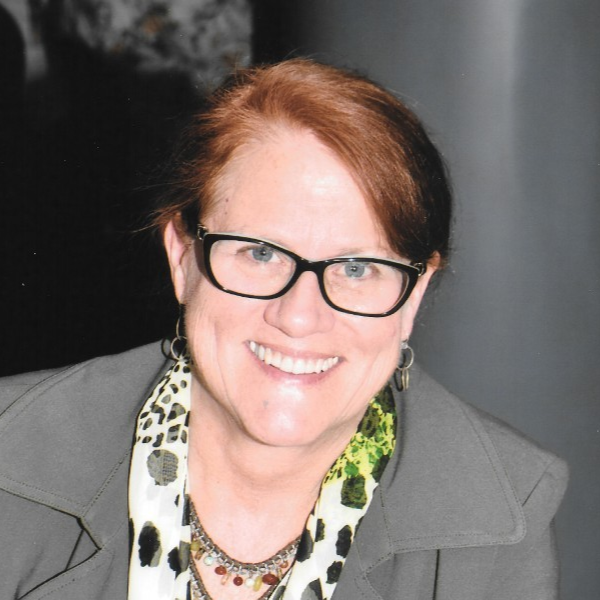
Margaret Koga Ward
Margaret Koga Ward has over 30 years of medical device experience, specializing in Product Development, Quality Management Systems, Internal and External Auditing, and Risk Management. She is currently an Independent Consultant, a Notified Body Auditor specializing in MDSAP and ISO 13485 audits, and an AAMI University faculty member. Her passion is helping companies achieve their quality management system and product development goals to advance their devices from concept through to commercialization within an FDA and ISO compliant quality system.
Ms. Koga Ward has served as a consultant for the FDA to develop and present quality management training courses for multiple divisions within the FDA.
Prior to becoming an independent consultant, she held various senior level project management, quality management system, and engineering positions leading cross functional teams throughout all phases of product development and quality system integration.
Ms. Koga Ward served as the Project Manager responsible for the integration, development, and commercialization of a novel, invasive device. She was also the senior consulting engineer for an Arizona based consulting firm; in this role she managed quality and product development projects for a wide range of Class I, II, and III medical devices including orthopedic, cosmetic, cardiac, ocular, and gastro-esophageal devices. She is an established subject matter expert for FDA regulations, ISO 13485, risk management, packaging, human factors, biocompatibility, and sterilization.
Ms. Koga Ward holds a Mechanical Engineering degree from California Polytechnic University San Luis Obispo.
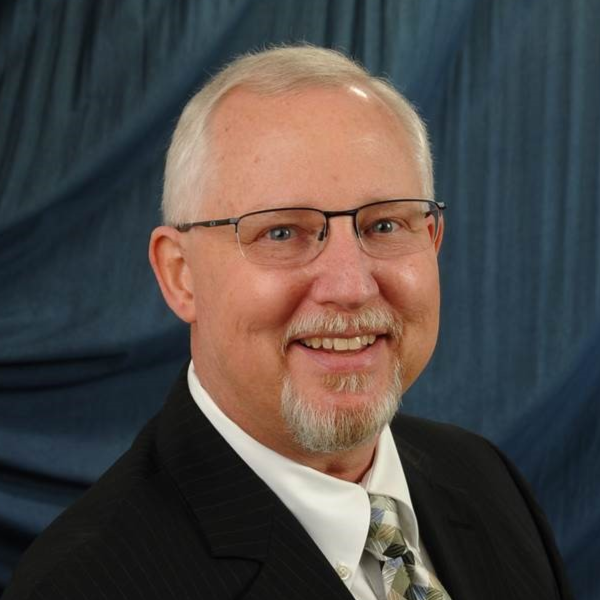
Lindsey Howard
Lindsey is currently the Principal at Lindsey Howard Consulting LLC. He brings over 42 years of broad Quality and Regulatory Affairs experience to AAMI’s educational programs. His career has spanned several industries including automotive, aerospace, drug, biologic, and multiple device companies (critical care, in vitro diagnostic, and companion diagnostic). His vast experience includes numerous start-up ventures involving implementation of complete Quality Management Systems and development of new products under Design Controls.
Prior to starting his own company, Lindsey held various leadership positions in healthcare companies, both large and small, including Abbott Laboratories, Life Technologies, Digene, Wellstat Biologics, and most recently retiring from QIAGEN as Vice President, Head of Global Regulatory Affairs.
Lindsey’s company is dedicated to helping organizations, of any size, to address challenges regarding Quality, Compliance, or Regulatory Affairs. We specialize in providing solutions that drive for a culture of quality and compliance, while optimizing the size and complexity of compliance systems. All with a clear focus to meet the specific needs of our client’s, their products, and/or services.
In addition to supporting AAMI as a trainer (i.e. QMS, Design Controls, and Validation), he has been actively involved in AdvaMed and while at QIAGEN sponsored the FDA’s Experiential Learning Program. He is also an ASQ member, ASQ Certified Quality Engineer, as well as a Certified Birkman® consultant.