AAMI Faculty
Quality Systems
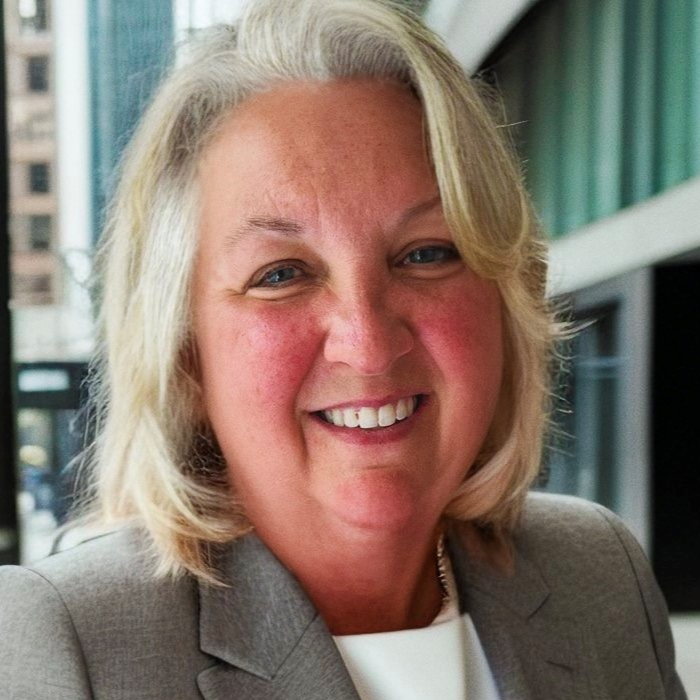
Tiea Theurer
Tiea is a quality and regulatory professional with experience in auditing, QMS, and medical writing relative to design and risk management. In her 20+ years of experience in the medical device industry, she has served in roles as project manager and design quality engineer. In these roles, Tiea acted as a change agent in QMS and DHF/DMR remediation efforts to resolve FDA 483 and notified body nonconformances for companies who were under warning letters or consent decree.
Tiea has performed 100+ audits as a Lead auditor for Notified Bodies to assess compliance with quality management system (QMS) standards (ISO 9001/13485) and regulatory requirements for the USA 21CFR820, EU (MDD/MDR, IVDD/IVDR), Canada (CMDCAS), and MDSAP jurisdictions (Australia-TGA, Brazil-Anvisa, Canada-CMDR, Japan-MHLW, and US-FDA). Tiea has experience with various technology types, such as, but not limited to software as a medical device, sterilization and sterile barrier systems, plastics, mechanical and electrical equipment and chemicals.
Based on these, Tiea is qualified for auditing most medical and IVD devices, with the exception of implantable devices. Tiea has working relationships with several private clients which required gap assessments and remediation activities of quality and regulatory documents relative to industry standards and country regulations.
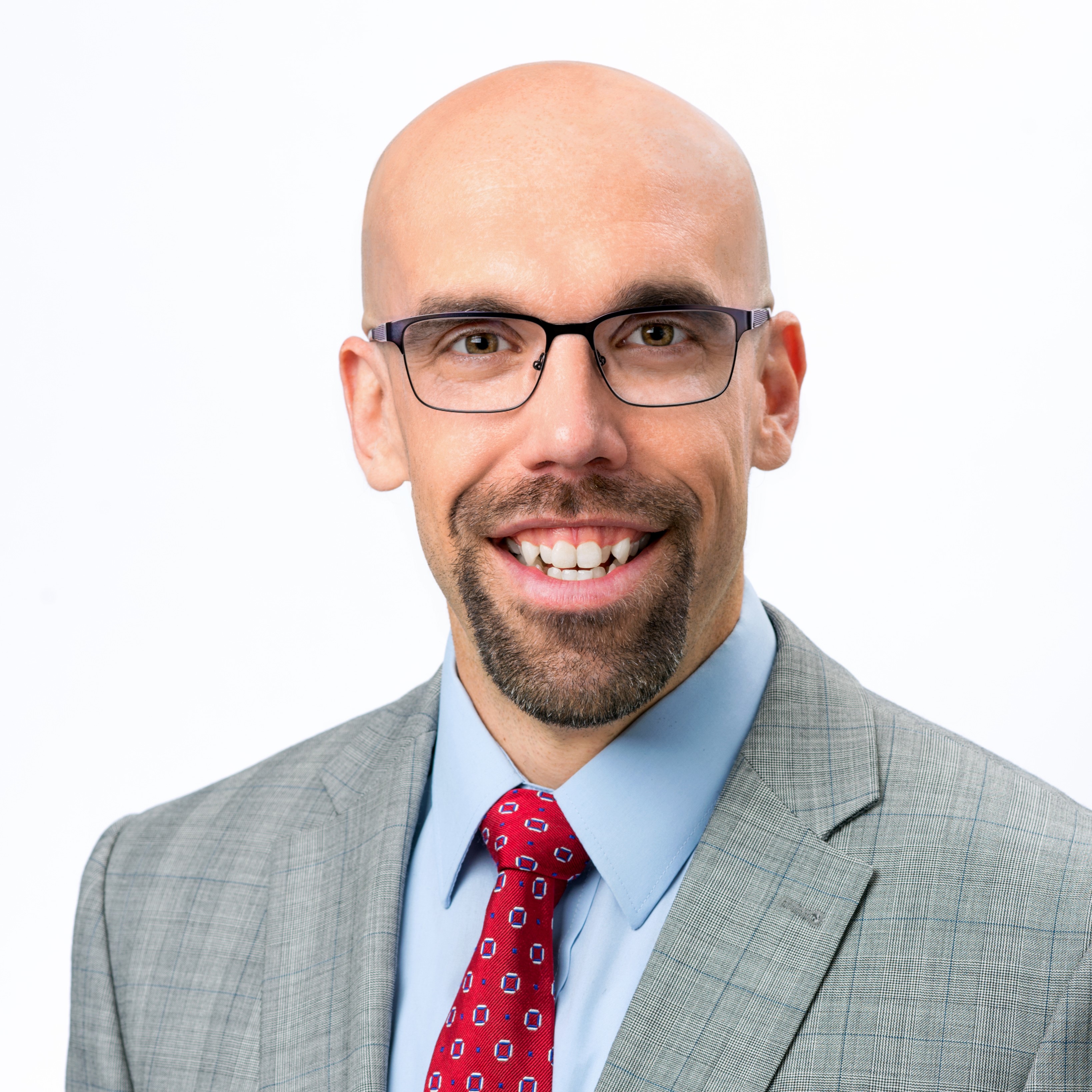
Mike Ziemelis
Mike Ziemelis currently works with Stryker in the Emergency Care business unit as a Senior Director within Research and Development. Mike and his teams are focused on the development of AEDs, defibrillators, patient monitors, and other therapeutic devices used within the emergency medical services space, hospitals, and the community.
Prior to working in his current role, Mike has held multiple roles within Stryker supporting different businesses that focus on various class I and class II medical devices. Mike has over 18 years of medical device experience in R&D, premarket RAQA, business development, and advanced manufacturing.
Mike is an experienced trainer within Stryker and with AAMI. As an active AAMI faculty member, Mike teaches the Quality System Requirements and Design Controls courses. Mike earned his Bachelors of Science in electrical engineering and his Masters of Science in Engineering management from Western Michigan University.
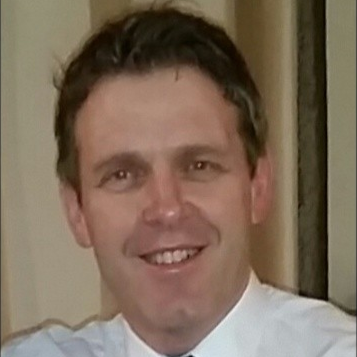
Gerard Manley
Gerald (Ger) Manley is a medical device and pharma industry consultant with +20 years’ industry experience and is owner & Director of G&C Creations Ltd.
G&C Creations ltd was founded in 2004. G&C Creations ltd has provided consultancy services in the medical device and pharmaceutical sector working for a host of different companies with considerable market share in the diagnostic, general medical devices, implants, API’s, Biologists etc. G&C Creations ltd has extensive experience in New product introduction, technical transfers, product launches, process improvement, Lean, end to end supply chain, Design Controls Quality system requirements, outsourced manufacturing and implementing full and partial Quality management systems.
In 2009 to complement the consultancy division of the business, G&C Creations added contract technical services which has +100 technical professionals supporting projects with various clients around Ireland and Europe
Qualification 93-95: National Cert. Electronics Eng
Institution - Tralee Institute of technology Ireland.
Qualification: 95-96 Diploma Mechanical and Electronic Engineering
Institution - Tralee Institute of technology Ireland.
Qualification: 96-98 Bachelor of Engineering Hons (1:1) Mechanical & Production Engineering
Institution - University of Limerick Ireland.
Qualification: 2000 National Cert. EH&S - Waterford Institute of technology Ireland.
Faculty Member of the Association for the advancement of medical instrumentation (AAMI) – Training Partner to the FDA
AAMI certified faculty for the following;
- Process Validation
- Design Controls
- QSR for 21CRF820 & ISO13485:2016
- Risk Management
Certified Lead auditor ISO13485:2016
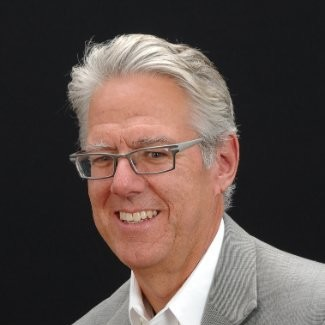
Andy Snow
Andrew has almost 40 years of experience managing quality, design and development for large medical device companies, start-ups and contract manufacturers. He has proven expertise in quality systems, risk management, design controls, requirements management, software life cycle processes and reliability engineering. He has a proven track record for developing risk management processes and systems for software and hardware device using ISO 14971. He has leveraged this expertise to help companies improve compliance, product quality and reliability. He has a BS degree in Biology from Fort Lewis College, a master’s degree in engineering from Northwestern and a graduate certificate in Systems Engineering from University of Arizona.
Andrew is currently a Quality and Regulatory Consultant to the Medical Device Industry Specializing in Improving Quality Management Systems. His skills and expertise include:
· Medical Device Quality and Regulatory – FDA 21 CFR part 820, Quality Systems Regulations and ISO 13485 Quality Management Systems for Medical Devices.
· Recognized industry expert in Risk Management using ISO 14971 and including integration with t=requirements for IEC 60601 and IEC 62304.
· Requirements lifecycle management including eliciting/formulating requirements, traceability and configuration management across the lifecycle.
· Design Verification, Design Validation planning and execution
· Process development, characterization and validation planning and execution.
· Supplier quality management and purchasing controls.
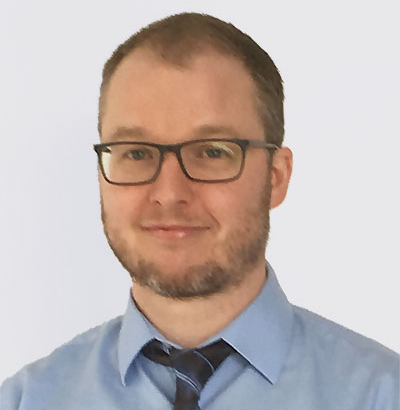
Sebastian Clerkin
Seb Clerkin is the founder of GMP Advisory Services, cofounder of CQT Solutions and a faculty member of the Association for the Advancement of Medical Instrumentation (AAMI). He currently provides quality system and regulatory consultancy to multiple clients within the Medical Device sector.
He has an excellent track record in providing consultancy, training and auditing. His main expertise is in the areas of Regulations, Quality Management systems, Design Controls, Software and Process Validation. He is a IRCA certified lead auditor and provides auditing services to multiple clients.
He has published articles in peer-reviewed journals on topics such as cleaning validation. He has a PhD from the University of Bristol, which involved studying the toxicological and biological effects of prosthetic implants and is a member of AAMI and RAPS.
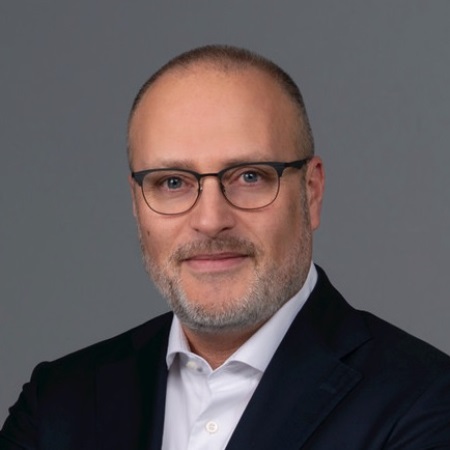
Mario Wijker
Mario Wijker is a seasoned quality and regulatory professional with over 30 years of experience in the medical device and in-vitro diagnostics industry. He started his career performing human genetic testing at the Free University of Amsterdam in The Netherlands.
Since then, he has held several positions in small, medium and large in-vitro diagnostics and medical device companies in all product classifications. In addition to roles in business development and strategic marketing, he has led global quality and regulatory organizations for 15 years and has developed and implemented quality systems in several companies.
He is an expert in quality remediation program and translating quality and regulatory requirements into actionable deliverables for a corporation. He is a certified ISO 13485:2016 and MDSAP lead auditor and has a degree in Biochemistry and Genetics.
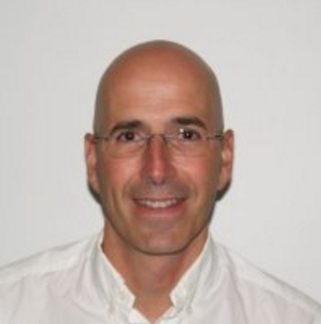
Philippe Joly
client firms to establish cGMP/QSR-compliant quality systems or to improve the efficiency of the existing ones. He has 10 years of experience in developing and delivering training on cGMP/QSR. Prior to this job, Philippe Joly has been involved in sales, marketing and product development for two international companies involved in the biopharmaceutical and medical device market.
Philippe Joly has a MS degree in Biochemistry and Microbiology and a Master's in Management and Marketing. He has led several workshops and task forces (Personnel qualification, cleaning validation, validation of computerized systems, risk management) for the two main French Pharmaceutical societies.
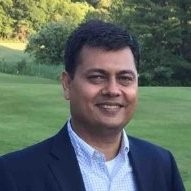
Samir Paliwal
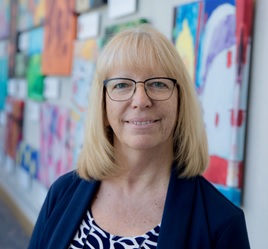
Tina Krenc
Tina is the Principal Consultant for KTA Compliance Consulting. She has over 40 years of medical device industry experience in a variety of organizations and functions including IVDs, software, hardware, combination products, and implantable medical devices. She has led employees in research and development, clinical research, operations technical support, and has over 25 years of quality assurance experience in multiple quality organizations.
As a consultant, Tina assists organizations with developing or improving their QMS to support the safety and effectivenss of their medical devices.
Tina serves as member of TC 210 ISO/IEC/ JWG1 on Application of Risk Management to Medical Devices and is the co-lead of the US TAG for ISO 14971. Tina is also a member of IEC SC 62A - Common aspects of electrical equipment used in medical practice. In addition, she is the ISO TC210 liaison for Risk Management subject expertise to ISO/TC212 - In-vitro Diagnostics Technical Committee.
Tina received a Master of Science in Product Design and Development from Northwestern University School of Engineering in 2006.
Tina has taught risk management for several organizations including Northwestern University Master of QARA program and AAMI. She teaches several AAMI University courses including Design Control, Quality Management Systems, Process Validation, and Risk Management.
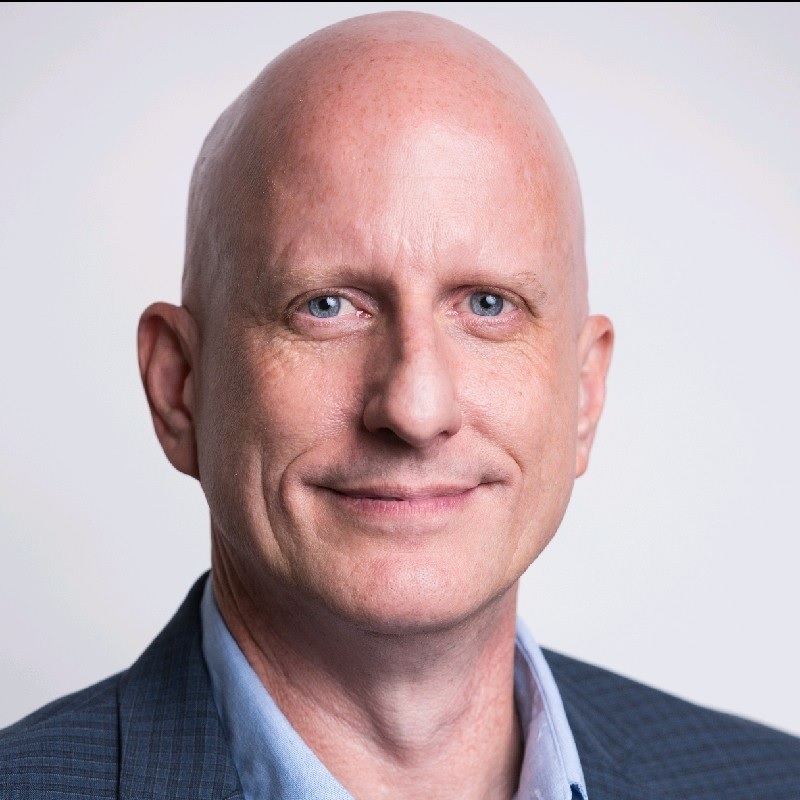
David Nelson
David has a background in Software Engineering and has 26+ years of experience developing and validating Medical Devices. He currently is an Associate Software Director for Boston Scientific Neuromodulation. His responsibilities include managing all aspects of software development and validation including security risk. In addition, David is a faculty member at AAMI and has been developing and instructing courses for more than 12 years.
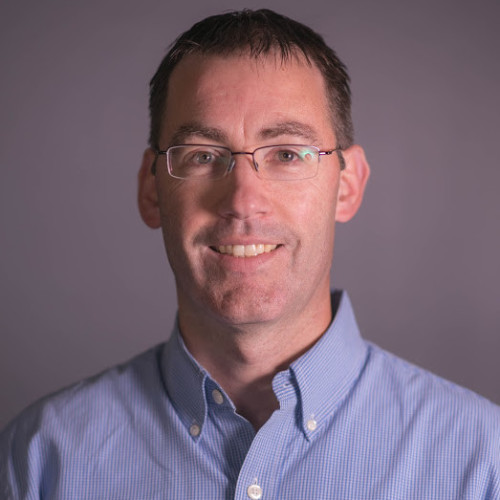
Eric Kruschke
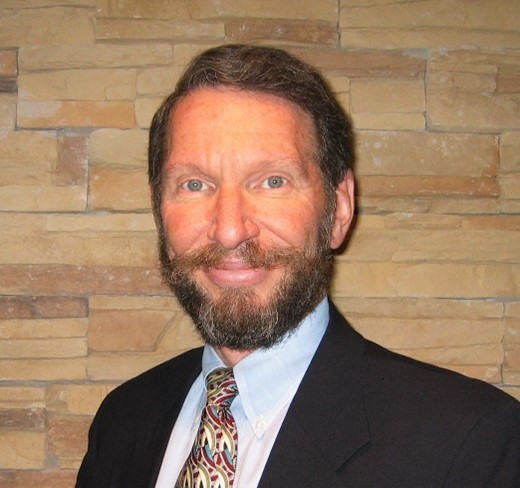
Peter Knepell
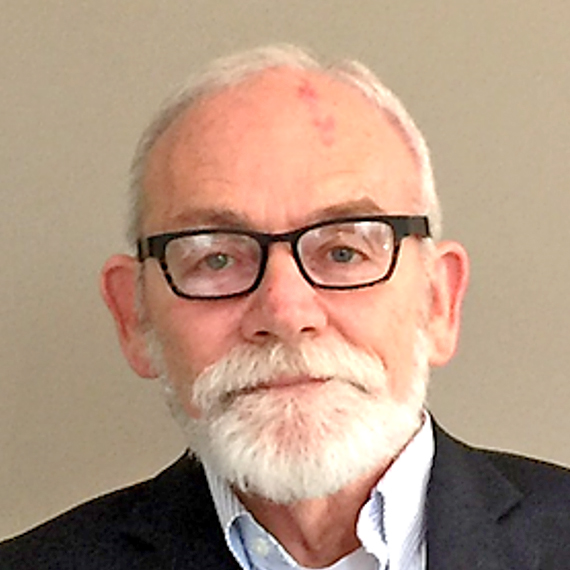
Jack Ward
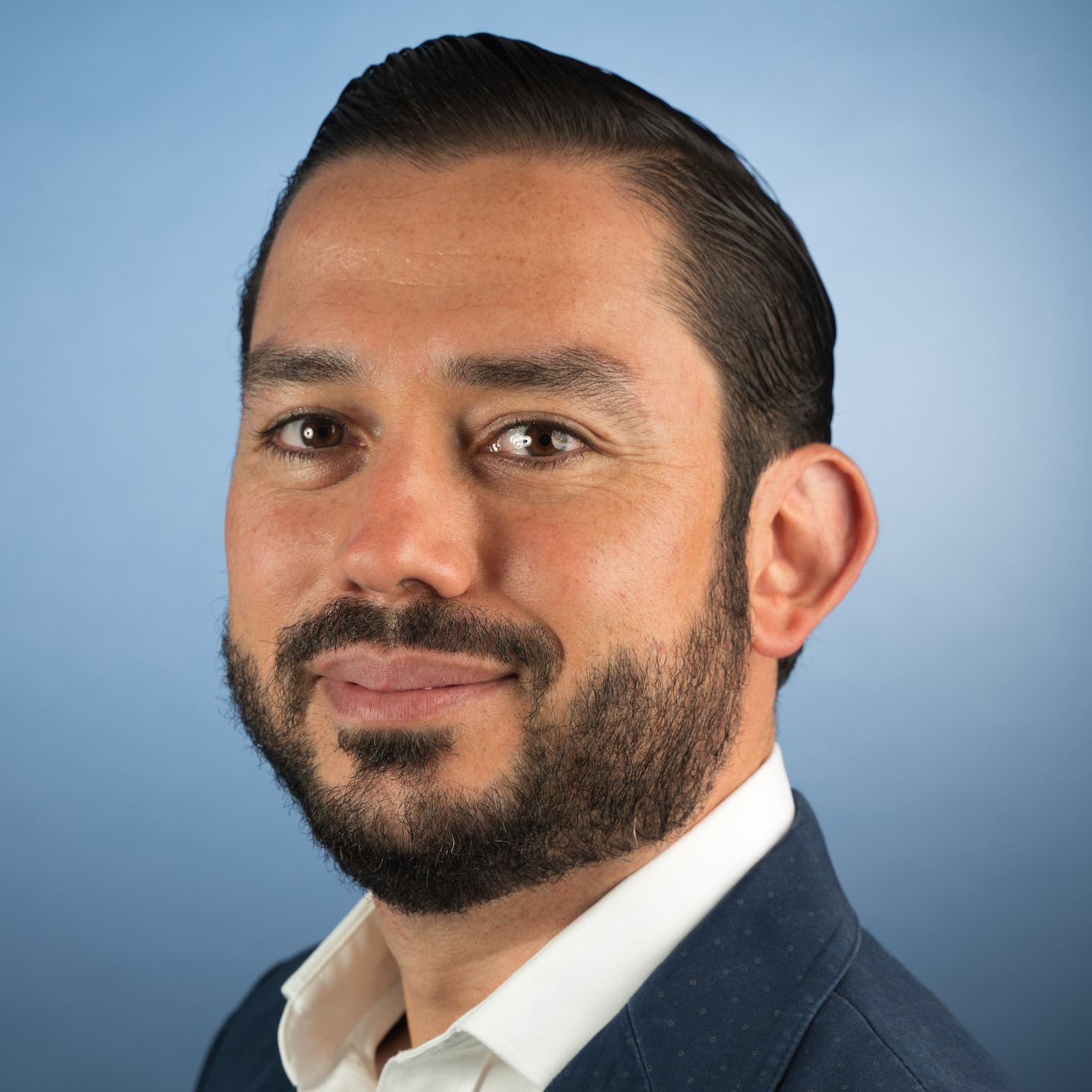
Pablo Montero
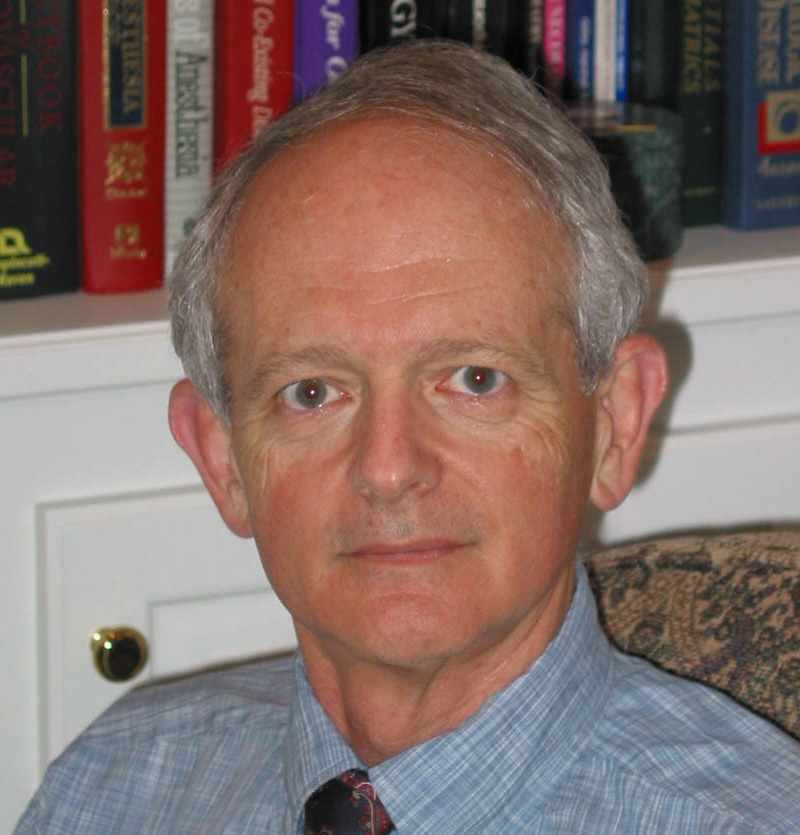
Ed Bills
During his career in medical devices, Mr. Bills has held a number of quality and regulatory affairs positions for major medical device companies, including a period as Corporate Director of Risk Management. He has over 39 years’ experience in the field of quality and regulatory affairs, including time as Director of Quality and Regulatory concurrently for four US sites. Currently he consults and provides training in the area of medical device quality, regulatory and risk management. With Stan Mastrangelo, he co-edited Lifecycle Risk Management for Healthcare Products: From Research Through Disposal published by PDA and has written extensively in the area of quality, regulatory, and risk management for medical devices and combination products.
ASQ has awarded Mr. Bills with Fellow status as well as Certified Quality Engineer, Certified Quality Auditor, Certified Manager of Quality and Organizational Excellence, and he is Regulatory Affairs Certified by the Regulatory Affairs Professionals Society. In his career he has given presentations nationally and internationally in the field of quality management and risk management.
Additionally, Mr. Bills serves in international standards work, assisted in completing the revision of the third edition of ISO 14971 risk management standard and the guidance ISO TR 24971:2020 as an international member of the technical committee. He also serves on the US national committee for the medical devices quality system standard, ISO 13485, as well as the medical bed standards, IEC 60601-2-52, IEC 60601-2-89, and the AAMI technical committee CP contributing to the combination products risk management guidance, AAMI TIR 105.
Mr. Bills has recently taught as part of the Quality Science Education program at The Wistar Institute, and LaSalle University under the Pathways for Patient Health program. He has previously taught at University of Southern California, the University of Washington, and Purdue University Southeast. He was also adjunct faculty at Virginia Tech in the Health Products Risk Management Graduate Program and assisted in development of that program.
Recently, Mr. Bills joined Gessnet as a Technical Advisor. He also serves on the Advisory Board of Product.
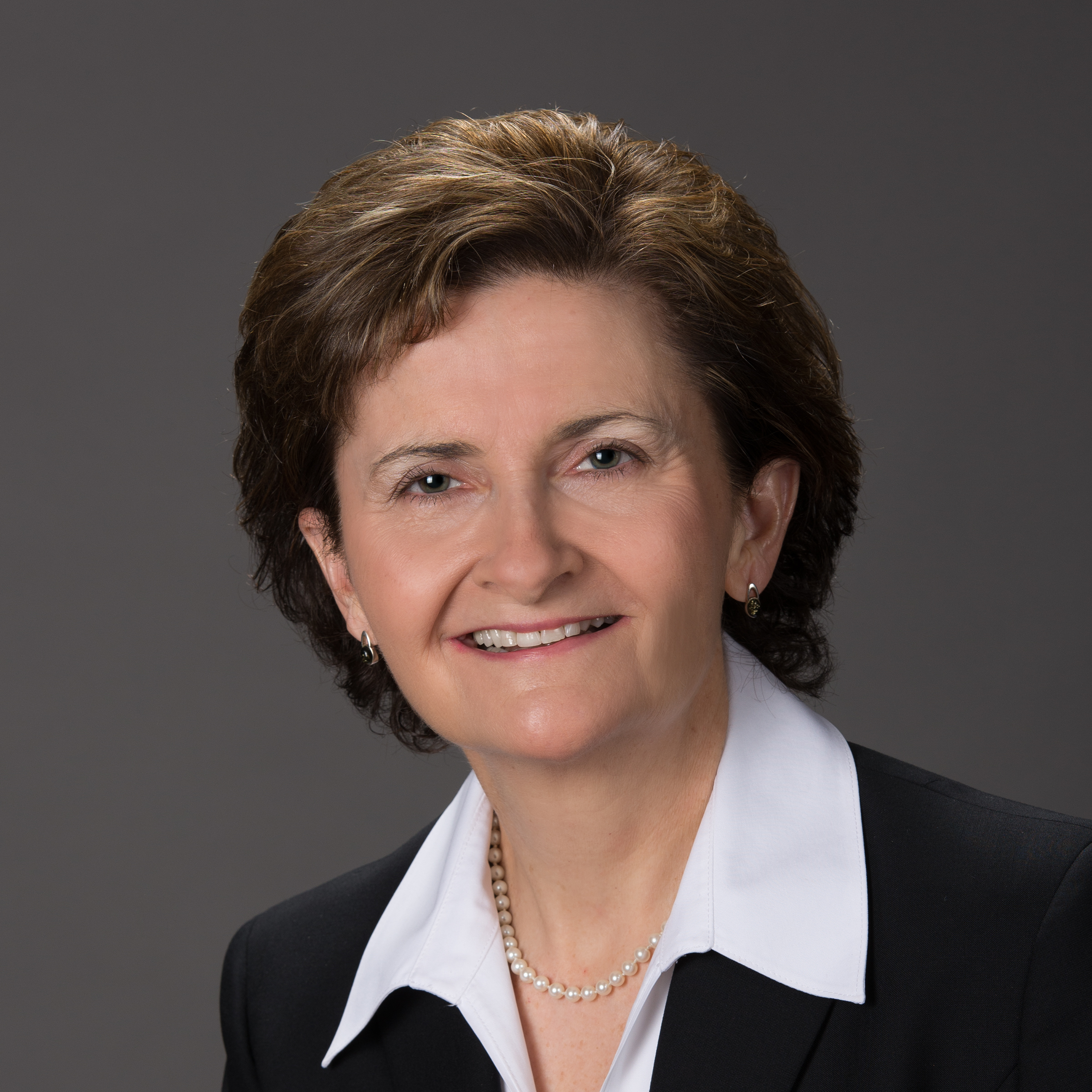
Annette Hillring
Annette Hillring has been an independent regulatory affairs consultant since 1998. Prior to consulting, she worked in the medical device industry with ophthalmic, cardiovascular and general hospital devices. She has over 40 years of experience in regulatory affairs, quality systems, clinical affairs and compliance. Her worldwide regulatory affairs responsibilities have included FDA and worldwide device submissions, Quality System Regulation compliance, ISO 13485 conformance, interpretation of all FDA regulations and policies, regulatory representation on new product development teams, due diligence assessments and product liability. She has also served as an expert witness for FDA and has extensive experience in software related FDA/industry guidance and standards-setting activities.
Ms. Hillring is Regulatory Affairs Certified and holds BA degrees in biology, microbiology and secondary science education
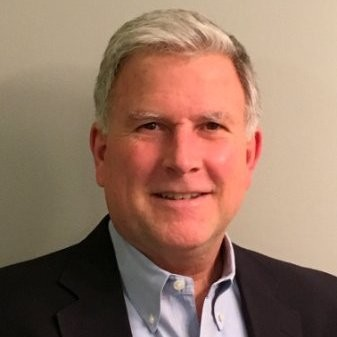
Mark Walker
Mr. Walker has been an instructor for the Association for the Advancement of Medical Instrumentation (AAMI) since 2012 which develops training and guidance with FDA for the use of medical devices. He currently serves on AAMI Medical Device Software Committee. Mr. Walker was a contributing author for The Quality System Compendium: CGMP Requirements and Industry Practice, Fourth Edition and also co-authored “Risk Management Tools” (Chapter 2) in the book “Risk Management Applications in Pharmaceutical and Biological Products Manufacturing”, published by John Wiley & Sons, Inc.
Mr. Walker has a Bachelor of Science degree and an Associate of Engineering degree in chemical engineering technology. In his free time, he volunteers with county emergency rescue service agencies providing technical rescue, emergency medical services and computer systems support.
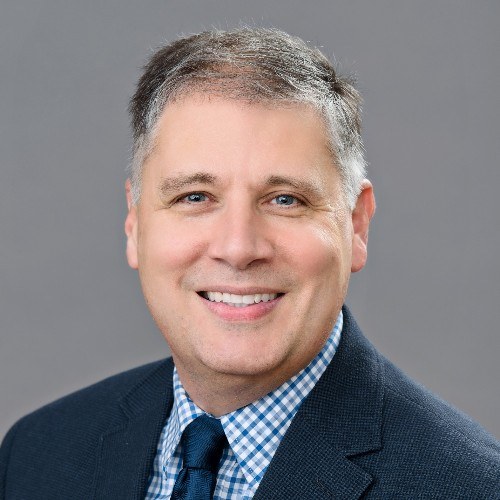
Mark Durivage
Mark Allen Durivage has worked as a practitioner, educator, and consultant. He is Managing Principal Consultant at Quality Systems Compliance LLC, ASQ Fellow, SRE Fellow, and an Expert Faculty Member for AAMI. He holds several certifications including CRE, CQE, CQA, CSQP, CSSBB, RAC (Global), and CTBS. Durivage has written several books available through ASQ Quality Press, published articles in Quality Progress, and is a frequent contributor to Life Science Connect.
Mark primarily works with companies in the FDA regulated industries (medical devices, human tissue, animal tissue, and pharmaceuticals) focusing on quality management system implementation, integration, updates, and training. Additionally, he assists companies by providing internal and external audit support as well as FDA 483 and Warning Letter response and remediation services.
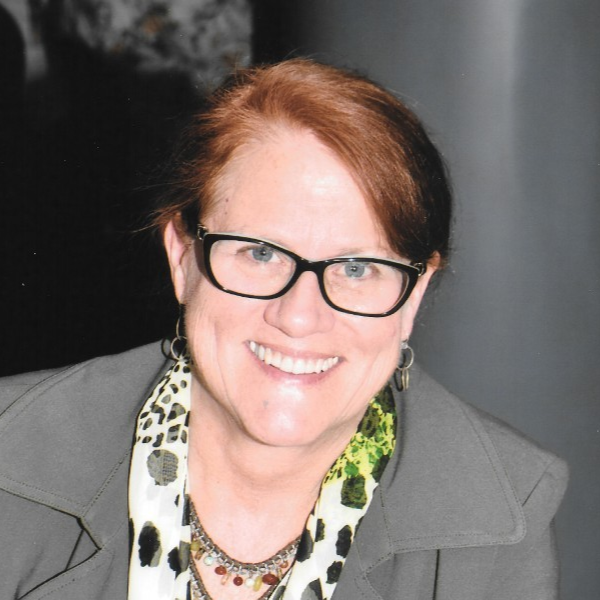
Margaret Koga Ward
Margaret Koga Ward has over 30 years of medical device experience, specializing in Product Development, Quality Management Systems, Internal and External Auditing, and Risk Management. She is currently an Independent Consultant, a Notified Body Auditor specializing in MDSAP and ISO 13485 audits, and an AAMI University faculty member. Her passion is helping companies achieve their quality management system and product development goals to advance their devices from concept through to commercialization within an FDA and ISO compliant quality system.
Ms. Koga Ward has served as a consultant for the FDA to develop and present quality management training courses for multiple divisions within the FDA.
Prior to becoming an independent consultant, she held various senior level project management, quality management system, and engineering positions leading cross functional teams throughout all phases of product development and quality system integration.
Ms. Koga Ward served as the Project Manager responsible for the integration, development, and commercialization of a novel, invasive device. She was also the senior consulting engineer for an Arizona based consulting firm; in this role she managed quality and product development projects for a wide range of Class I, II, and III medical devices including orthopedic, cosmetic, cardiac, ocular, and gastro-esophageal devices. She is an established subject matter expert for FDA regulations, ISO 13485, risk management, packaging, human factors, biocompatibility, and sterilization.
Ms. Koga Ward holds a Mechanical Engineering degree from California Polytechnic University San Luis Obispo.
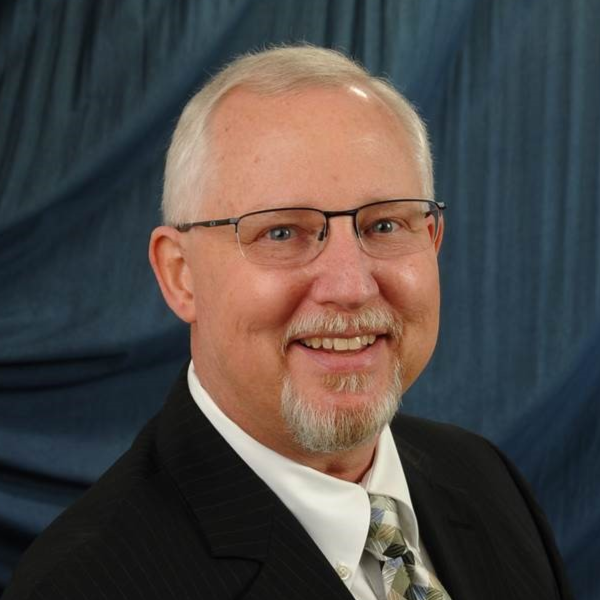
Lindsey Howard
Lindsey is currently the Principal at Lindsey Howard Consulting LLC. He brings over 42 years of broad Quality and Regulatory Affairs experience to AAMI’s educational programs. His career has spanned several industries including automotive, aerospace, drug, biologic, and multiple device companies (critical care, in vitro diagnostic, and companion diagnostic). His vast experience includes numerous start-up ventures involving implementation of complete Quality Management Systems and development of new products under Design Controls.
Prior to starting his own company, Lindsey held various leadership positions in healthcare companies, both large and small, including Abbott Laboratories, Life Technologies, Digene, Wellstat Biologics, and most recently retiring from QIAGEN as Vice President, Head of Global Regulatory Affairs.
Lindsey’s company is dedicated to helping organizations, of any size, to address challenges regarding Quality, Compliance, or Regulatory Affairs. We specialize in providing solutions that drive for a culture of quality and compliance, while optimizing the size and complexity of compliance systems. All with a clear focus to meet the specific needs of our client’s, their products, and/or services.
In addition to supporting AAMI as a trainer (i.e. QMS, Design Controls, and Validation), he has been actively involved in AdvaMed and while at QIAGEN sponsored the FDA’s Experiential Learning Program. He is also an ASQ member, ASQ Certified Quality Engineer, as well as a Certified Birkman® consultant.
Human Factors
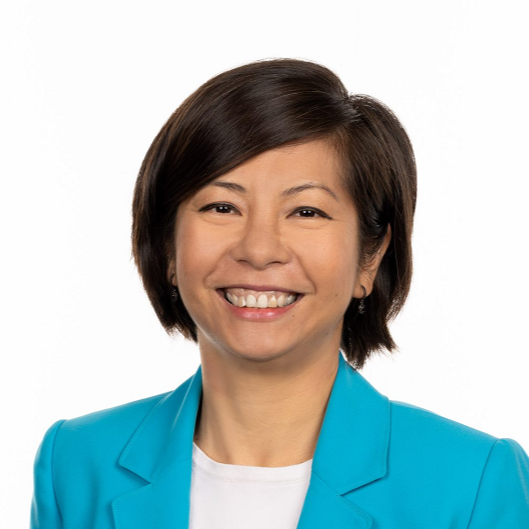
QuynhNhu Nguyen, MS
With over 17 years of experience in both consulting and FDA regulatory review evaluations, QuynhNhu Nguyen is the Director of Human Factors and Regulatory Strategy (HURAS) at Kymanox.
QuynhNhu has over 15 years of FDA regulatory science and evaluation experience with human factors, medication errors, and product design and development, reviewing 900+ medical products (devices, drugs, biologics, and combination products) that covered all therapeutic areas from various phases starting with investigational product applications to marketing applications to post approval supplements.
QuynhNhu has about 2 years of HF regulatory consulting with Kymanox and has supported 45+ projects serving small, medium, and large pharmaceutical companies in ensuring comprehensive HF program executions with data-driven regulatory strategies and “Right First Time” submissions.
QuynhNhu earned a Master of Science Degree in Systems Engineering from Johns Hopkins University and a Bachelor’s degree in Biomedical Engineering from George Washington University.
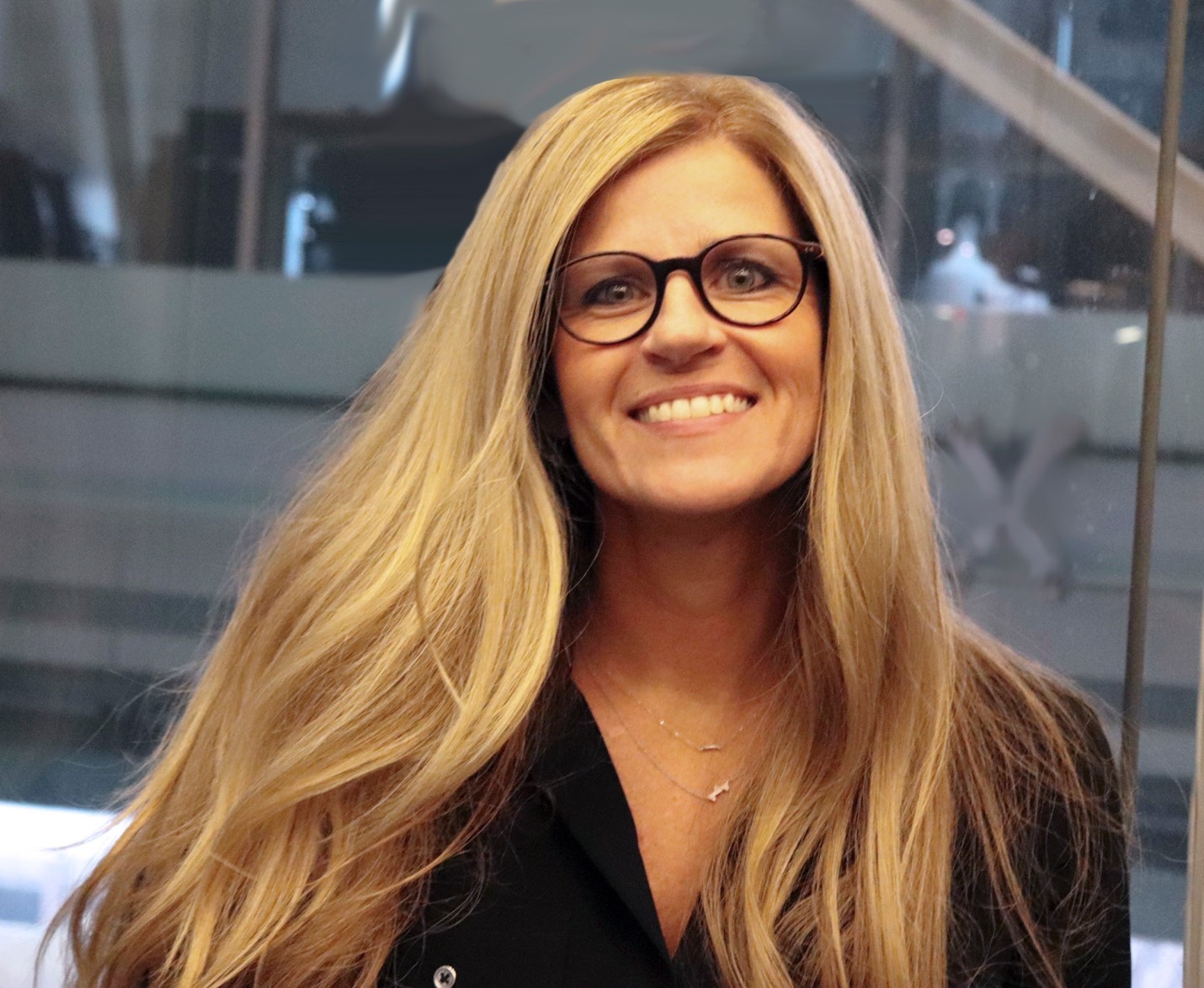
MaryBeth Privitera
Dr. Mary Beth Privitera, M.Design, FIDSA, is internationally known as an expert in medical product design, specifically in the area of applied human factors. She is a Professor at the University of Cincinnati’s Department of Biomedical Engineering and works collaboratively among the Colleges of Medicine, Engineering and Design. She is a consultant to the medical device industry with expertise in user interaction design and human factors. Additionally, she serves as faculty and co-chair of the Association for the Advancement of Medical Instrumentation’s Human Engineering Committee.
As a Professor at the University of Cincinnati’s Department of Biomedical Engineering, she is a Co-Founder of the Medical Device Innovation and Entrepreneurship Program. Her previous academic appointments include industrial design and in the Department of Emergency Medicine.
She has worked on devices which are intended for use across the practice of medicine and in home health situations. Her current research focuses on applied ergonomics and design interpretation. She has conducted contextual inquiry studies throughout the hospital with results intended to inform the design of devices, including physiologic monitoring and clinical decision making, software-based tools including intraprocedural augmented reality. In addition, she currently has had research funding supported by the Gates Foundation and US FDA CDER Division. She is a Fulbright Scholar in collaboration with the University of Nottingham.
She has authored several peer reviewed articles and a books titled “Contextual Inquiry for Medical Device Design,” promoting best practices for phase zero medical device development. Her 2nd book, edited and written in collaboration with AAMI Human Factors faculty is titled “Applied Human Factors in Medical Device Design.” This book aims at bringing all references and best practices together in one resource compendium.
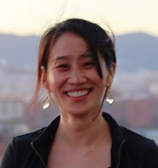
Rita Lin, MS, RAC
Rita has effectively managed medical device designs from concept to commercialization. She applies her technical and regulatory backgrounds to coordinate teams across multiple disciplines and departments. Rita has successfully led efforts to develop new digital health products while at Vigor Health, execute design modifications on spine devices while at Stryker, and help clear and approve hundreds of medical devices and combination products while at the FDA.
During her career, Rita has earned several certifications and awards, including the Stryker Innovation award, FDA Quarterly awards, Six Sigma Green Belt, and RAC. She is also expert faculty for the AAMI Human Factors for Medical Devices and 510k/De Novo training courses, and is a recurring speaker for the Human Factors and Ergonomics Society and Clemson University College of Engineering.
Rita graduated from Duke University with a Bachelor’s and Master’s degree in Biomedical Engineering.
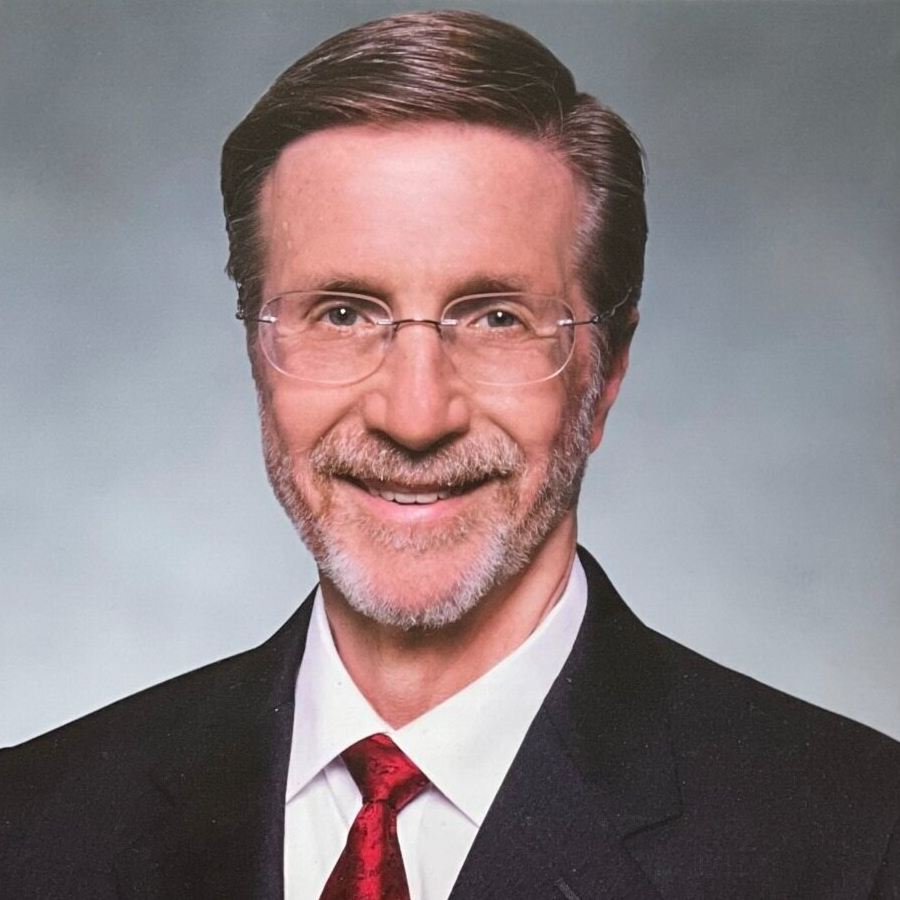
Edmond W Israelski
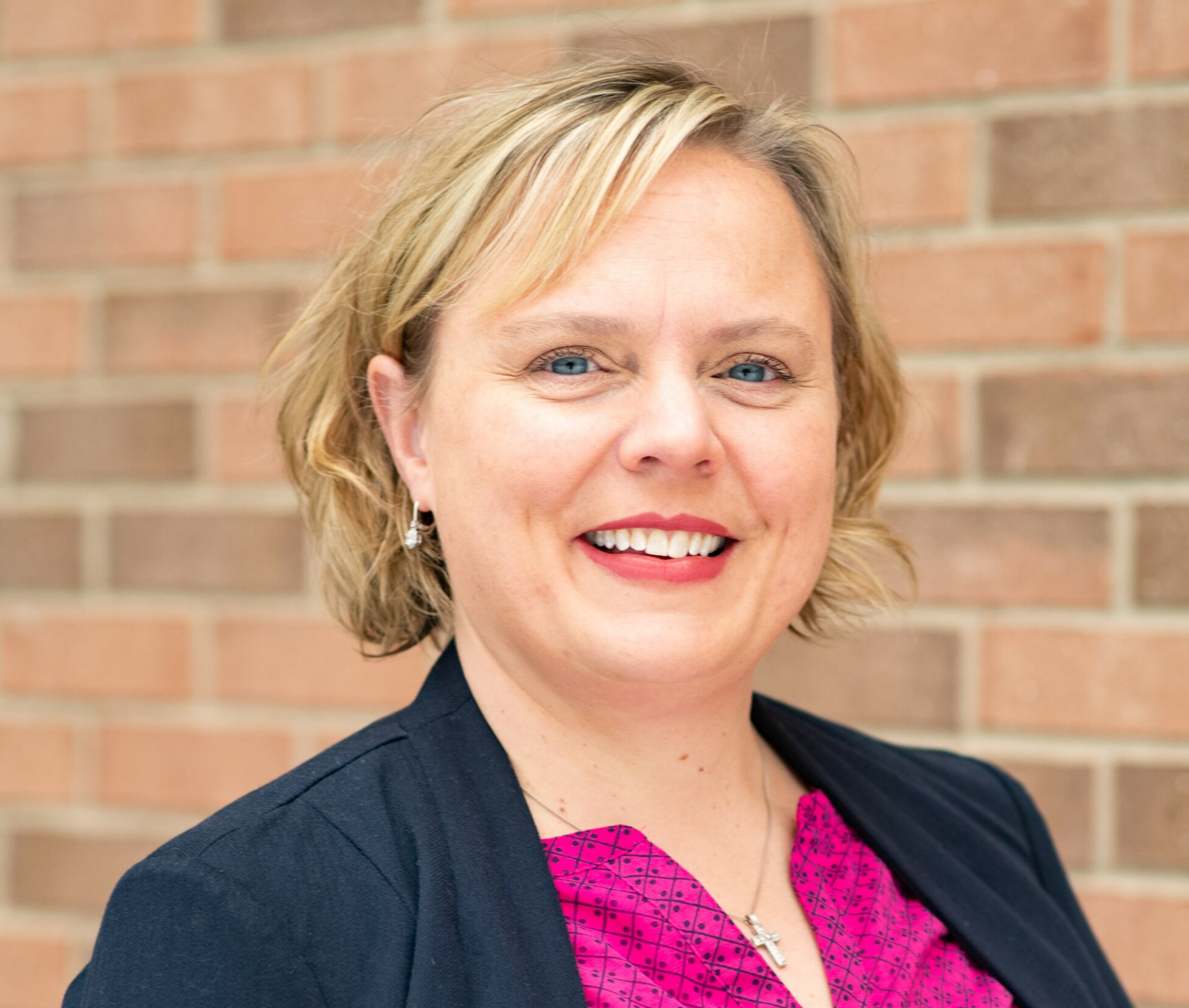
Melissa Lemke
Melissa Lemke is the founder and Principal Human Factors Engineering and Accessibility Advisor with Human Ability Designs, a human factors consultancy that supports client organizations in achieving human factors regulatory success and meeting user interface optimization goals throughout the pre-market and post-market design process. Melissa is dedicated to helping clients develop and bring to market medical products that are safe, effective, and usable for people of all abilities through applying sound human factors engineering strategies and methods.
Melissa is a Biomedical Engineer with over 20 years of experience designing successful human factors regulatory strategies, leading cross functional teams, and executing human factors analyses of medical devices, combination products, training and labeling. She also is a lay caregiver for her brother with spinal cord injury.
Formerly, Melissa built and managed the human factors services of Agilis Consulting Group, managed the Accessibility and Usability Testing Laboratory at Marquette University, and was a researcher and instructor with the University of Wisconsin at Milwaukee.
Melissa is an active member of the Human Factors and Ergonomics Society (HFES) as well as the Association for the Advancement of Medical Instrumentation (AAMI). She serves on AAMI’s Human Factors Engineering and Home Care and EMS Environments Committees. She is a contributing author to the original HE75: Human Factors Engineering - Design of Medical Devices, including lead co-author of the accessibility considerations section. More recently, Melissa led the committee updates of the revised HE75 for the sections on Accessibility and Devices Used in Non-clinical Environments by Laypersons and contributed to human factors industry publications including, Applied Human Factors in Medical Device Design (2019) and Development of Biopharmaceutical Drug-Device Products (2020).
-square790d0413-9c18-4d5a-9a29-d121a407232e.jpg?sfvrsn=8c40b99e_1)
Tressa J Daniels
9fde33c9-5ef6-4ae8-80e1-71ca135317c6.jpg?sfvrsn=f5985d2_3)
Merrick Kossack
Merrick Kossack serves as a Research Director for Emergo by UL’s Human Factors Research & Design (HFR&D) team. For over 25 years, Merrick has helped companies develop processes and strategies to address their human factors engineering needs, particularly for complex and high-risk systems. His areas of expertise include integrating human factors engineering into established design and development processes, conducting complex usability studies, and advising on human factors strategy to satisfy regulatory needs. In addition, he helps clients develop their use-related risk analyses, human factors reports, and other key documents required for regulatory submissions. Merrick has developed and taught courses on human factors in medical device development and delivered numerous presentations on the subject. He is a contributing author to the book Applied Human Factors in Medical Device Design (2019). Merrick is a member of the Association for the Advancement of Medical Instrumentation (AAMI) Human Factors Engineering subcommittee as well as IEC TC 62/SC 62A JWG4, both responsible for the creation of human-factors-related standards and guidance. He is also a member of the AAMI faculty staff responsible for teaching their Human Factors for Medical Devices course. Merrick earned an M.S. degree in Human-Machine Systems Research from the Georgia Institute of Technology and a B.S. degree in Industrial Engineering from the University of Illinois. In 2020, Merrick was inducted into UL’s William Henry Merrill Society as a Distinguished Member of Technical Staff.
Sterilization
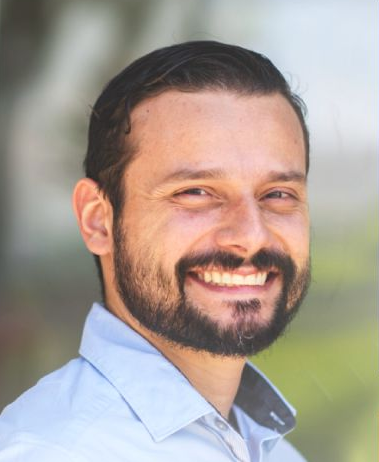
Roberto Zumbado
Roberto Zumbado is the Head of Technical Services for Philips IGTD.
Roberto is experienced in Medical Devices, Ethylene Oxide, Moist Heat, and radiation sterilization, Control Environment Rooms, Calibrations, Process, Equipment Validation and Laboratory Management.
Roberto has led the startup and implementation of the first EO in house sterilization site in Costa Rica and lead different sterilization optimization processes for different manufacturing sites.
He graduated from the University of Costa Rica as a Microbiologist and Chemical Analyst and has a master’s degree in industrial engineering, he also has a certification as Certified Biomedical Auditor and Certified Quality Manager from ASQ. He also has a certification as a Certified Sterilization Specialist on Ethylene Oxide from AAMI.
Before working with Philips, Roberto worked with companies such as Hologic and Baxter.
Roberto has published in The American Society of Tropical Medicine and Hygiene and has participated as a speaker in conferences around the world.
He also teaches Industrial Microbiology at the University of Costa Rica and supports optimization projects for medical device manufacturers as a consultant.
He is currently member of ASQ, AAMI and EOSA.

Deborah Havlik
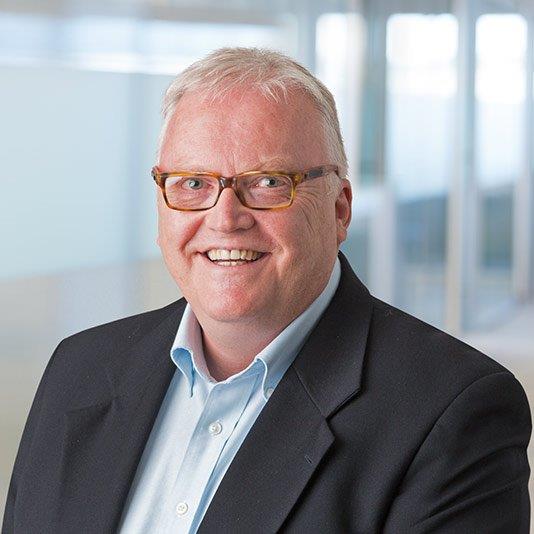
Kevin O'Hara
Kevin is the Director of Radiation Physics at Sterigenics with corporate responsibility for measurement and calculation of absorbed dose associated with the radiation treatment of product, such as sterilization of healthcare instruments. Kevin holds almost 30 years of experience in radiation physics and radiation dosimetry within a highly technical industry. He is actively involved in numerous industry committees, task forces and working groups. As a Working Group Member, Kevin represents Canada on ISO TC 198 WG2 Radiation Sterilization. He is also a member of the AAMI Sterilization Standards Committee, WG2 – Radiation Sterilization; ASTM Subcommittee E61 Dosimetry for Radiation Processing; and Chair or Co-chair of ISO/ASTM 51707 Estimating Uncertainties, 51275 Radiochromic Film, E2232 Mathematical Methods. Kevin is a Former President/VP, Radiation Process Simulation and Modelling User Group (2002 – 2010). Over his career, Kevin has been published many times.
Expertise: Radiation Sterilization Expert, Radiation Dosimetry, Mathematical Modelling, Hockey
Publications
“A Comparison of Gamma, E-beam, X-ray and Ethylene Oxide Technologies for the Industrial Sterilization of Medical Devices and Healthcare Products,” published by Gamma Industry Processing Alliance (GIPA) and International Irradiation Association (iia), 2017
Chapter on Gamma Technology, in “Food Irradiation Research and Technology, Chapter: Dosimetry for Food Processing and Research Applications, IFT Press, Blackwell Publishing, 2nd Edition, 2014
“Evaluation of Tracers and Contrast Agents in Optical Molecular Imaging,” a compilation of numerous publications and the potential impact on Medical Isotopes, 2009.
Biological safety in the context of backward planetary protection and Mars Sample Return: conclusions from the Sterilization Working Group, International Journal of Astrobiology, External Subject Matter Expert (2021)
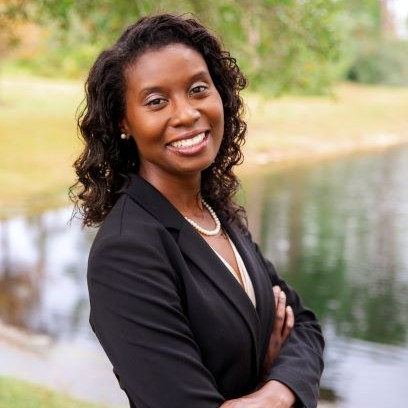
Samantha Hodge
With more than 15 years of sterility assurance experience in the healthcare technology space, Samantha is a dedicated professional who is passionate about safe, effective, and compliant solutions to industrial sterilization processes.
Samantha started her journey as a contract research technician working on R&D programs for the Vision Care division of Johnson & Johnson.
Eventually, she transitioned to Medtronic where she has served as a sterility assurance SME in controlled environments, laboratory operations, and terminal sterilization of disposable and reusable medical devices.
Sam holds a Bachelor of Science in Chemistry with a minor in Mathematics from the University of North Florida as well as a number of certifications which include Registered Microbiology (RM) from the U.S. National Registry of Microbiologist, ISO 9001/ISO 13485 lead auditor certification from Oriel STAT A Matrix, Green Belt certification from Medtronic in Design for Reliability and Manufacturing (DRM) – Design for Six Sigma (DFSS), and CISS in EO and radiation from AAMI ACI.
She is currently the Senior Director of Sterility Assurance at Medtronic and is set to complete her MBA May 2024 from the College of William & Mary – Raymond A. Mason School of Business.
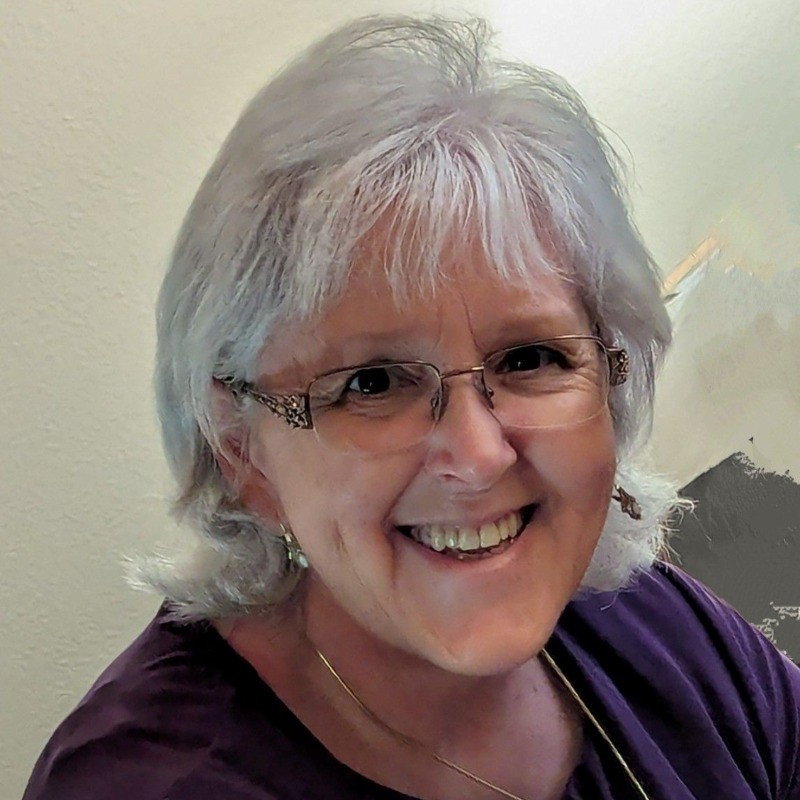
Gerry A O’Dell
Gerry O’Dell has a master’s degree in microbiology from the University of South Florida. She has been in the health care products industry since 1983 and is owner and President of Gerry O'Dell Consulting for over 25 years. Gerry O'Dell Consulting is a consulting firm that works to assist companies of all sizes and in all phases of business development in the areas of sterilization (all major sterilization modalities and novel sterilization methods), environmental monitoring, laboratory and other related compliance areas for single-use medical devices, reusable medical devices, biologics, and pharmaceuticals.
Gerry O’Dell has participated in the sterilization standards process for over 35 years and is a member of most of the AAMI sterilization standards related working groups as well as several of the working groups related to reusable medical device processing. She is past co-chair of the AAMI Industrial Ethylene Oxide Sterilization Working Group and the AAMI Industrial Moist Heat Sterilization Working Group. She currently is a member of the U.S. Sub-TAG for ISO/TC 198/WG 1 (ethylene oxide), WG3 (moist heat), and WG8 (microbiological methods).
Gerry O’Dell was selected as an AAMI Fellow in 2019. She is a Certified Industrial Sterilization Specialist for EO, Radiation, and Moist Heat as well as a Registered Microbiologist with the National Registry of Microbiologists in Consumer Products & Quality Assurance. She was a co-author on “The Application of ISO 11138-7 for Industrial Ethylene Oxide Sterilization Qualification” in the January 11, 2023 issue of the AAMI Array and has authored “Sterilization Validation Principles” in The Medical Device Validation Handbook and “Sterilization by Ethylene Oxide” in Microbiology and Sterility Assurance in Pharmaceuticals and Medical Devices.
.png?sfvrsn=b831cfb1_1)
Clark Houghtling
Clark Houghtling is the Vice President of Business Development & Technical Affairs for Cosmed Group, Inc. Cosmed was founded in 1981 to sterilize medical devices and spices. The company grew to be among the largest contract sterilization companies in the United States, until it divested its five medical device sterilization locations in 2005 to focus on food safety. The company continues to use various technologies to pasteurize raw agricultural commodities in facilities dedicated to those purposes. The company reentered the medical device sterilization market in 2012 performing contract sterilization, along with selling sterilization equipment (i.e. sterilizers, control systems, scrubbers, and related accessories).
Clark’s varied background includes extensive knowledge in sterilization technologies, related microbiological and chemical testing, business development, plant and quality management, medical device manufacturing, sales, marketing, and regulatory affairs. Prior to this position, Clark worked in various upper management positions for companies including Comet ebeam Technologies, Synergy Health, Stryker Orthopaedics, Microtest Labs, Steris, Mallinckrodt, and Ethox. He holds a Bachelor of Science degree in Biology from the State University of New York at Geneseo, and attended graduate school in Biology at Niagara University.
Clark has taught many courses and is a frequent lecturer to many varied groups including the Food and Drug Administration (FDA), the Association for the Advancement of Medical Instrumentation (AAMI) (where he is an AAMI Fellow and serves as an instructor for the Industrial Sterilization for Medical Devices and the Industrial Ethylene Oxide Sterilization for Medical Device courses), the International Society for Pharmaceutical Engineers (ISPE), the Center for Professional Advancement (CPA), and for various companies. He is a member of the Sterilization Standards Committee at AAMI, the American Society for Microbiology (ASM), and a senior member of the American Society for Quality (ASQ). In addition, he served as Vice President, and as Treasurer, of the Ethylene Oxide Sterilization Association (EOSA), and is a former ASQ Certified Quality Auditor (CQA). Clark also participated in helping formulate the AAMI Certified Industrial Sterilization Specialist (CISS) program, and was in the first group to achieve the CISS certification in Ethylene Oxide, Radiation, and Moist Heat.
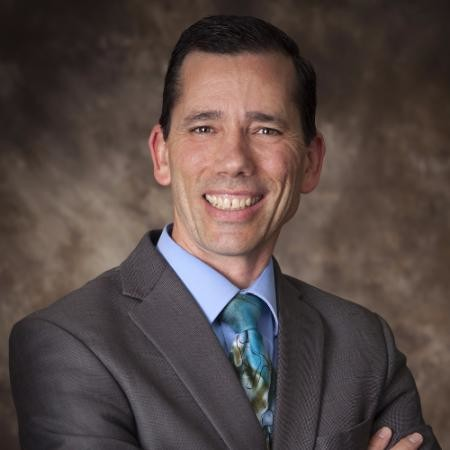
Martell Winters
Mr. Winters received a B.S. in microbiology with a minor in chemistry from Brigham Young University. He has been at Nelson Laboratories for over 25 years testing and consulting regarding radiation sterilization, bioburden/sterility testing, microbiological process validation, allograft tissue and pharmaceutical products. He is currently a Director of Science for Nelson Laboratories. Mr. Winters serves on many AAMI Sterilization Standards Working Groups and represents the U.S.A. at ISO meetings for microbiological methods, aseptic processing and vaporized hydrogen peroxide sterilization. He is also on the AAMI Sterilization Standards Committee and is the AAMI liaison to the AATB Standards Committee. In 1995 he received his Registered Microbiologist (RM) certification, and in 2001 his Specialist Microbiologist (SM) certification in consumer products and quality assurance microbiology from the U.S. National Registry of Microbiologists. In 2018 he helped develop the program, and then certified as an AAMI Certified Industrial Sterilization Specialist in radiation (CISS-RAD).
Software and Cybersecurity
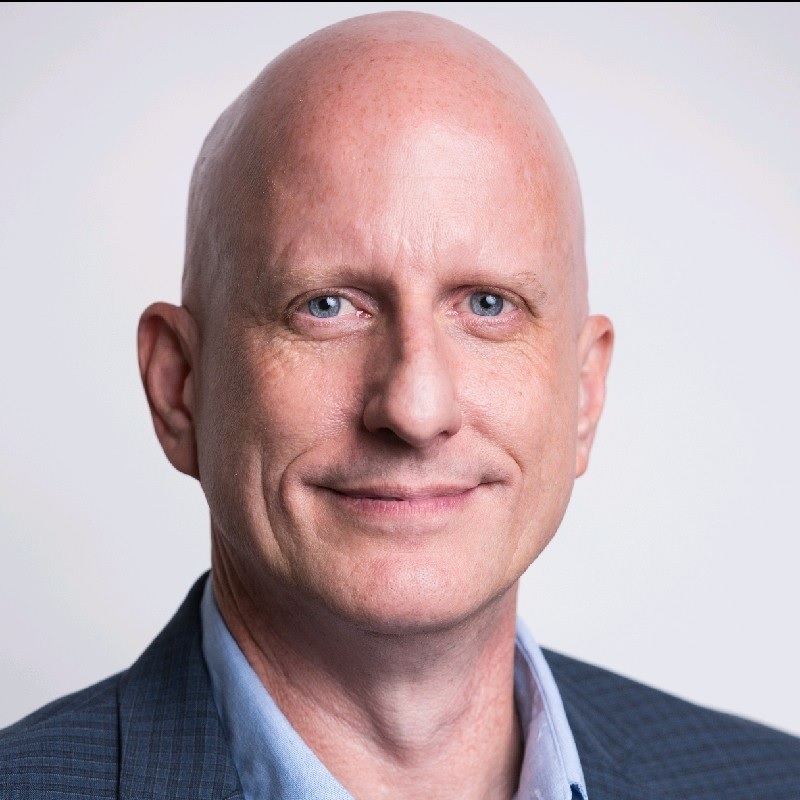
David Nelson
David has a background in Software Engineering and has 26+ years of experience developing and validating Medical Devices. He currently is an Associate Software Director for Boston Scientific Neuromodulation. His responsibilities include managing all aspects of software development and validation including security risk. In addition, David is a faculty member at AAMI and has been developing and instructing courses for more than 12 years.

Jeremy Jensen
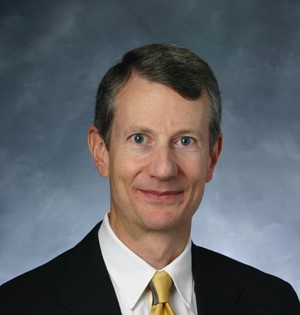
Mike Russell
Mike Russell is a Partner with SoftwareCPR®. He provides services such as Quality Management System assessments and efficiencies, regulatory filing assistance, development process improvements, and leadership coaching and training. He is an expert in business agility and “agile and compliant” process transformation. Mike served on the TIR working group that created the AAMI TIR45- 2012 Technical Information Report Guidance on the use of Agile practices in the development of medical device software.
Mike combines expertise serving as both a C-level executive, including as Chief Operations Officer for a top 60 U.S. bank, and as a trusted advisor to CEOs and other top leaders at diverse organizations in multiple industries. This has provided him with first-hand experience dealing with many opportunities and challenges facing leaders today, especially with rapid change and digital transformation. For example, while leading a product division, Mike introduced changes that resulted in improved productivity by 15%, cut time-to-market by up to 67%, and reduced defects by over 50% in flagship products processing of over $80 billion in financial transactions per year.
His experiences cover 48 U.S. states, Puerto Rico, U.S. Virgin Islands, and 20+ countries. He has spoken internationally and written on many subjects, including transformation and business agility, in his book Wrong Until Right – How to Succeed Despite Relentless Change. He also has been a reviewer for other authors’ books and publications. He has taught at both undergraduate and graduate levels and was a Lean Startup Week mentor.
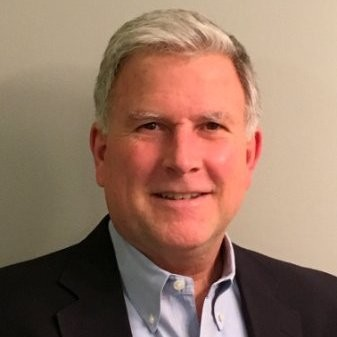
Mark Walker
Mr. Walker has been an instructor for the Association for the Advancement of Medical Instrumentation (AAMI) since 2012 which develops training and guidance with FDA for the use of medical devices. He currently serves on AAMI Medical Device Software Committee. Mr. Walker was a contributing author for The Quality System Compendium: CGMP Requirements and Industry Practice, Fourth Edition and also co-authored “Risk Management Tools” (Chapter 2) in the book “Risk Management Applications in Pharmaceutical and Biological Products Manufacturing”, published by John Wiley & Sons, Inc.
Mr. Walker has a Bachelor of Science degree and an Associate of Engineering degree in chemical engineering technology. In his free time, he volunteers with county emergency rescue service agencies providing technical rescue, emergency medical services and computer systems support.
Healthcare Technology Management (HTM)
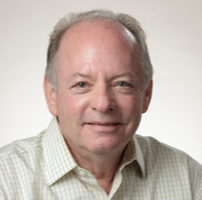
Mike Kritzman
CEO
SkillNet
Mike Kritzman is the Founder and CEO of SkillNet and a recognized thought leader in skill management and skill-based learning.
Previously, he held leadership roles at Oracle and Ernst & Young, where he was tracking workforce skills with spreadsheets. Determined to modernize skill tracking, Mike founded SkillNet, a cloud-based platform that helps firms become skill-based organizations.
The SkillNet platform identifies skill gaps, tracks certifications, and creates personalized training plans to solve gaps and help organizations build a highly skilled workforce.
Mike has worked extensively in Healthcare Technology Management (HTM), partnering with firms like Kaiser Permanente, Brigham and Women’s Hospital (BWH), and Sodexo to streamline skills and certification tracking for technical teams.
SkillNet collaborates with industry leaders like the College of Biomedical Equipment Technology to enhance learning programs with skill data and maximize learning impact and deliver a rapid return on investment.
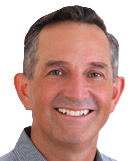
Bo Burick
Principal
DoorTwo
FOSTER A FUTURE OF INSPIRED LEADERSHIP
Bo Burick seeks to elevate others. Since stepping onto the grounds of the United States Air Force Academy as a cadet in 1989, Bo has relished opportunities to lead and guide others. With a mindset toward excellence and collaboration, Bo is highly skilled at identifying high-potential leaders and developing effective teams. Known for stress-testing leaders, the Academy pushed Bo to his physical, mental, and intellectual limits. The Academy taught Bo the importance of a collaborative team and a leader’s inherent responsibility to elevate each member to be their personal best. This experience sparked a life passion for continued growth and service to others, paving the way for his current coaching and leadership training practice with Door|Two.
"Inside every person are untapped, hidden strengths waiting to be harnessed for personal growth and leadership excellence."
— Bo Burick
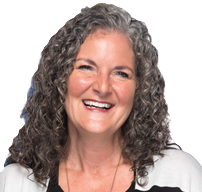
Anna Baldwin
Principal
DoorTwo
DOOR | TWO
ANNA BALDWIN
REFOCUS, REINVENT, AND REJUVENATE
Anna Baldwin is an award-winning Operations Strategist with 20-plus years of professional experience. She is a Principal at Door|Two. As the Chief Operating Officer at Innovative Dining Group and Native Foods Café, Anna was responsible for providing the strategic and tactical operational leadership to leverage the passion and culture to achieve sales, earnings, and growth targets. She is grounded in systemic processes to refocus, reinvent, and move sales and performance to the highest level.
"I would describe this program and the coaching with Anna as not prescriptive, asking you to reflect and to consider if you are making the best choices based upon leadership goals."
— Director / Program Participant
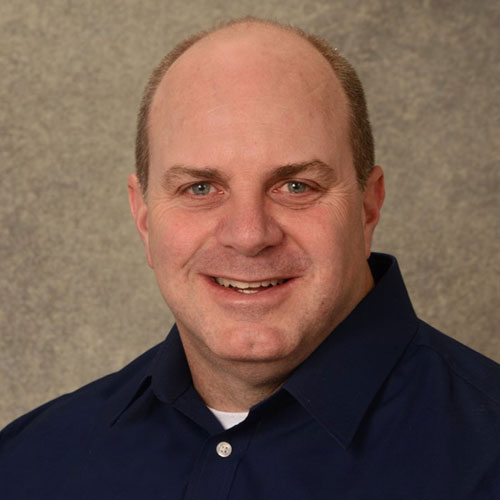
David Scott
•Started as a student in Biomed in 1989
•Started Colorado Association of Biomedical Equipment Technicians (CABMET) CBET Study Group in 2004
•2009 AAMI/GE Biomed of the Year
•Member of 2012 MD Publishing Department of the Year
•Featured as “Tech of the Month” in Medical Dealer Magazine
•Served as CABMET President, Vice President, Board Member
•Provided CBET Review at MD Expo
•AAMI CBET Review Presenter
•A.S. Degree in Sports Medicine Technology
•Military trained BMET (US Army)
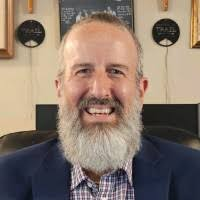
Jeffrey Ruiz
Jeff Ruiz CHTM, is a Senior Site Manager with Trimedx serving Sparrow Health System and Holland Hospital. Jeff also serves as a member of the Editorial Advisory Board with 24x7 Magazine and has
authored numerous articles for the magazine. Jeff is also a member of the AAMI Faculty supporting the CHTM Study Group. Jeff received his ACI CHTM certification in 2018. He has Associate’s Degree in
Electrical and Biomedical Engineering Technology as well as a Bachelor’s in Quality Management. Long Form Bio:
Jeff Ruiz, CHTM is a Senior Site Manager with Trimedx serving Sparrow Health System and Holland Hospital. Jeff has been with the Trimedx organization since 2010. Jeff was the winner of Trimedx’s Making a Difference Value aware in 2019. Jeff also helped led his Holland Team as Trimedx’s HCT Best Site in 2019. Jeff serves as a member of the Editorial Advisory Board at 24x7 Magazine as well as contributing author. Jeff is a member of AAMI’s faculty supporting the CHTM study group. Jeff was a contributing member of the CHTM exam review in 2019.
Prior to Trimedx, Jeff worked for Home Care of Michigan as Director of Operations. Jeff has been in the Healthcare Industry since 1985. Jeff was also Adjunct instructor at Muskegon Community College from 2017 to 2022 for Biomedical Instrumentation. Jeff was able to update the program which included expanding the program from one semester course to two.
Jeff has earned an Associates in Electric Engineering Technology from Lawrence Technical University, Associates in Biomedical Engineering Technology from Schoolcraft College, and a Bachelor’s Degree in Quality Management from the National Graduate School of Quality Management. Jeff has received his ACI CHTM certification in 2018.
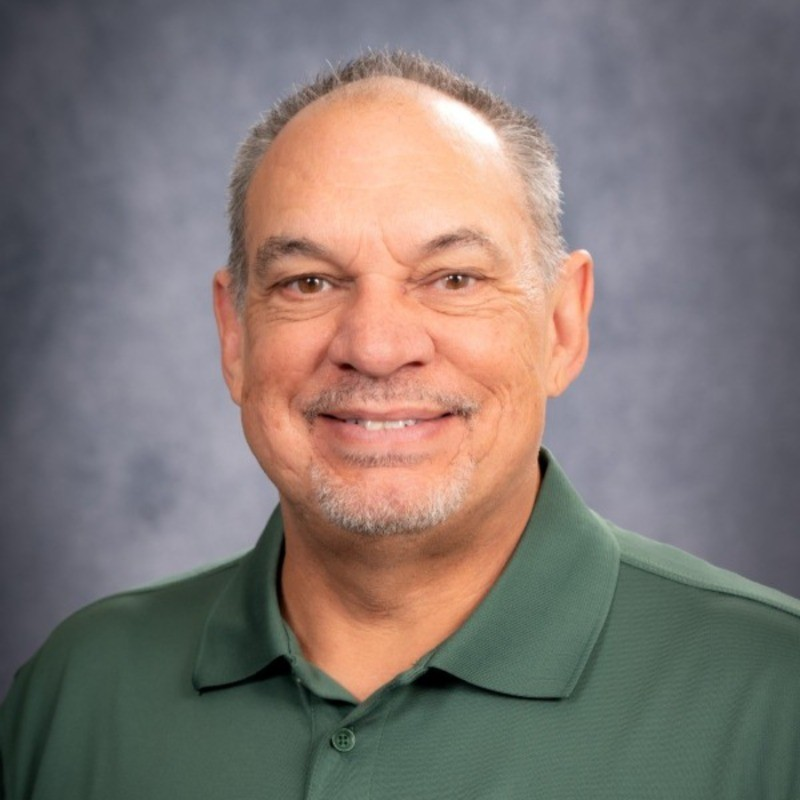
Donald Armstrong
•Been a HTM professional for over 40 years
•Has taught the CBET (Certified Biomedical Equipment Technician) Review Course since 2020
•Graduated with a bachelor's from Kaplan University in 2010
•CBET since 2006 and CHTM since 2016.
•Had Held Biomed, Lead Biomed, Customer Quality Manager, CBET and Sr. Manager roles throughout my career but my heart and soul are being a Biomed (especially in the OR).
•Current Role is Technical Training Manager for Renovo Solutions
•Previously worked at Stanford Health Care, GE Healthcare and UCSF.
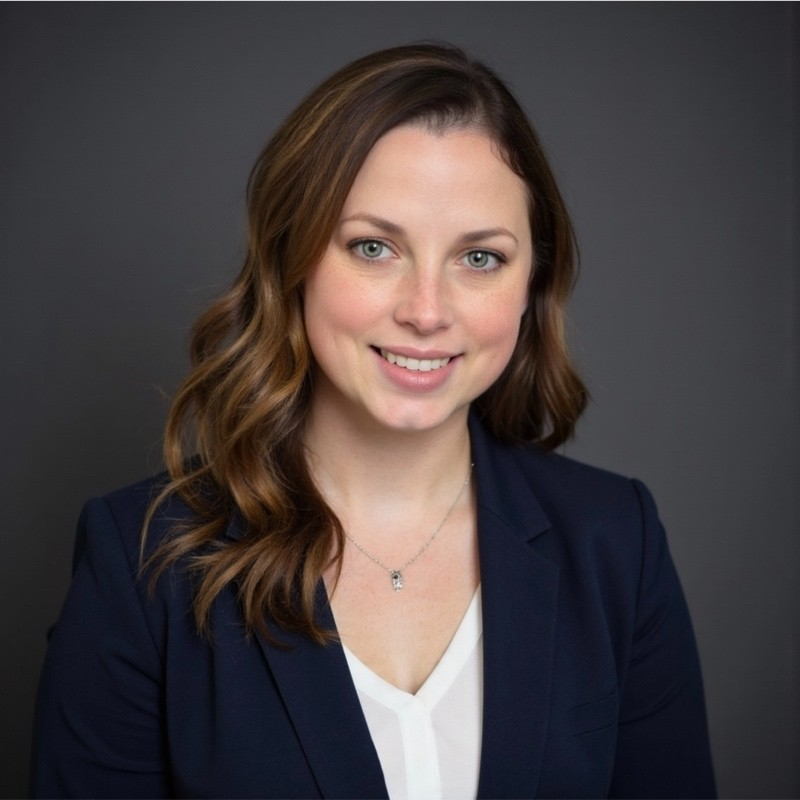
Angela Bennett
Angela received her Bachelors of Science in Applied Science Technology, Biomedical Technology from Thomas Edison State University. She received her CHTM from AAMI/ACI in May 2023. She started as a BMET in the United States Army in 2014. She has won awards to include the AAMI Young Professional Award in 2020 and the ACCE Professional Achievement in Management/Managerial Excellence Award in 2023. She is on the AAMI HTLC- Young Leadership committee and is an AAMI instructor for the new AAMI CHTM course. She has written a few pieces for HTM media outlets and has been a guest on a few HTM based podcasts.
Regulatory
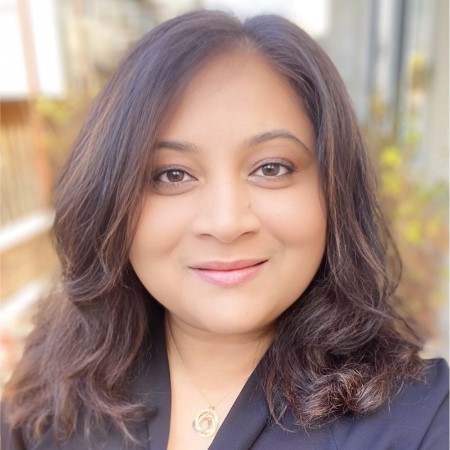
Pooja Kartik
As a seasoned Leader with over 23 years of experience and a Vice President of Quality & Regulatory, Pooja drives excellence in Medical Technologies, including digital health and combination products. Her expertise lies in building strong teams, coaching and mentoring teams to excel, negotiations, and alignments with stakeholders including regulatory bodies worldwide, global quality & regulatory strategy, regulatory compliance, risk management, software design quality and post-market surveillance.
With a hands-on approach, she has established quality systems based on FDA QSR (device and combination products), EU MDR/IVDR, EU MDD, ISO 13485 and MDSAP for class 1, class 2, and class 3 medical devices, strategized and lead FDA inspections, and global audits, lead teams conducting design quality activities, digital applications program portfolio management, product quality activities, CAPAs, recalls, management reviews, led remediation strategies and execution post FDA inspection/notifying body audits, and guided stakeholders through global regulatory and compliance.
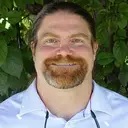
Rob Packard
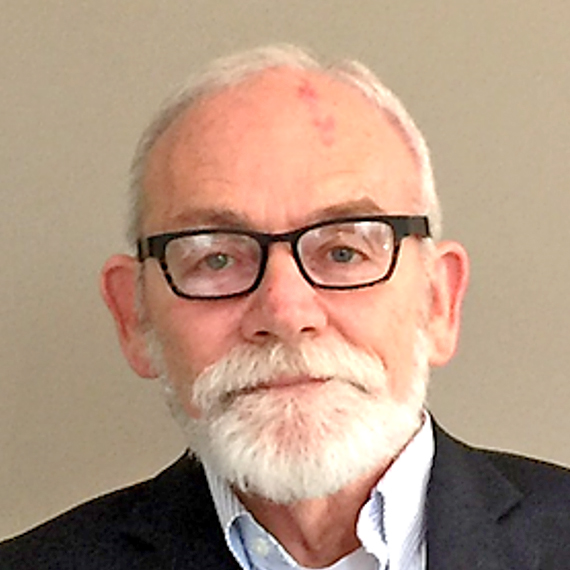
Jack Ward

Mary Vater
Mary Vater is a Medical Device Consultant at Medical Device Academy. Mary earned her degree in Biomedical Engineering from Wichita State University. Prior to Medical Device Academy, Mary served time in both Engineering and Quality roles at Biomedical Devices of Kansas and was a Regulatory Strategist at Cerner Corp. At Medical Device Academy, Mary assists companies in both Quality and Regulatory assignments. Mary has worked on over 30 devices’ 510(k) clearances and has participated in countless Pre-Submission meetings with the FDA. Mary’s experience spans many different technologies including SaMD (Digital Health, Mobile Apps, AI/ML Contouring, Computer Aided Detection/Diagnosis/Triage), In Vitro Diagnostic Devices, Reprocessed Devices, Electromechanical Devices, Implants, Dental Products, Surgical Planning, Surgical Tools, and more. Mary is an expert in Medical Device Quality Management Systems and serves as interim Quality Manager for several of her early-stage start-up clients. Mary helped develop and teaches the AAMI 510(k)/De Novo and the Lead Auditor courses. In her free time, Mary enjoys camping and boating with her husband, baby son, and two dogs. At home, she can be found trying new recipes in the kitchen or tending to her chickens and garden.