Strategic Design & Implementation of a Cost of Poor Quality Program
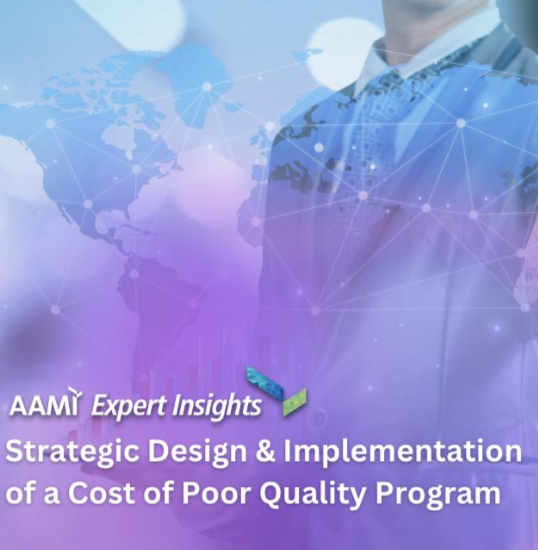
Upcoming Virtual Courses
Overview
Hidden costs from poor quality can significantly impact your company's profitability. Our specialized training program is designed to uncover and address the Cost of Poor Quality (COPQ), which encompasses all financial losses due to product defects and service failures, including scrap, rework, repair, and warranty claims. This course will help you understand how COPQ affects your profit margins and how to communicate these impacts effectively to management.
By understanding and applying the principles of COPQ, you will learn to identify opportunities for improvement, shift focus from merely fixing problems to preventing them, and implement effective corrective actions. The course will guide you through defining quality goals, assessing current capabilities, gathering and validating quality cost data, and comparing the costs before and after implementing changes. Equip yourself with the skills and tools needed to transform your approach to quality management and drive significant, sustainable cost savings for your organization. Enroll now to master COPQ and enhance your company's operational excellence.
Objectives
Over the course of (4) hours, the attendee/learner will be able to:
- Understand all contributors to the Cost of Poor Quality (COPQ), including prevention, appraisal, internal failure, and external failure costs.
- Model and analyze COPQ costs for each contributor, utilizing appropriate tools and techniques to evaluate their impact on overall financial performance.
- Create clear, transparent, and actionable reports on COPQ, effectively communicating the findings to stakeholders to facilitate informed decision-making and drive improvement actions.
Who Should Attend?
This course is designed for anyone involved in managing, measuring, or improving quality and who needs to understand and address the financial implications of poor quality.
For Example:
- Quality Managers and Engineers: Professionals responsible for overseeing quality management systems and ensuring product or service standards are met.
- Operations Managers: Individuals who manage production and operational processes and are keen on reducing inefficiencies and costs associated with poor quality.
- Finance Professionals: Those involved in budgeting and financial analysis who need to understand the financial impact of quality issues on the company’s bottom line.
- Process Improvement Specialists: Experts focused on continuous improvement initiatives and looking to optimize quality and reduce costs.
- Supply Chain Managers: Professionals managing suppliers and procurement who need to address quality issues impacting external and internal costs.
- Senior Executives and Decision Makers: Leaders who make strategic decisions and need insights into how quality affects profitability and resource allocation.
- Consultants: External advisors who assist companies in improving quality and reducing costs and would benefit from a deep understanding of COPQ to provide informed recommendations.
Virtual Training Information
Faculty
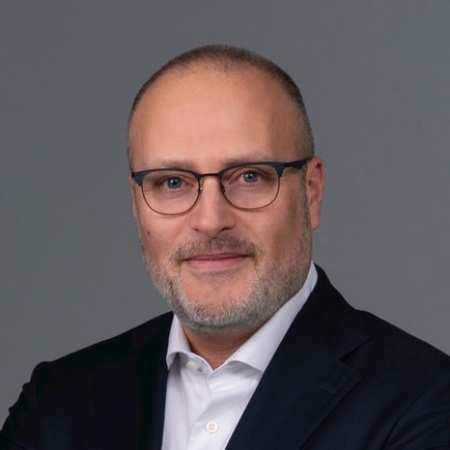
Mario Wijker
Mario Wijker is a seasoned quality and regulatory professional with over 30 years of experience in the medical device and in-vitro diagnostics industry. He started his career performing human genetic testing at the Free University of Amsterdam in The Netherlands.
Since then, he has held several positions in small, medium and large in-vitro diagnostics and medical device companies in all product classifications. In addition to roles in business development and strategic marketing, he has led global quality and regulatory organizations for 15 years and has developed and implemented quality systems in several companies.
He is an expert in quality remediation program and translating quality and regulatory requirements into actionable deliverables for a corporation. He is a certified ISO 13485:2016 and MDSAP lead auditor and has a degree in Biochemistry and Genetics.